All guns work on the same basic principle. Something is burned inside a tube, and the burning produces gas which pushes the projectile out. Traditionally, this something was gunpowder, also known as black powder, and by extension pretty much all solid propellants1 for guns are known as powder.
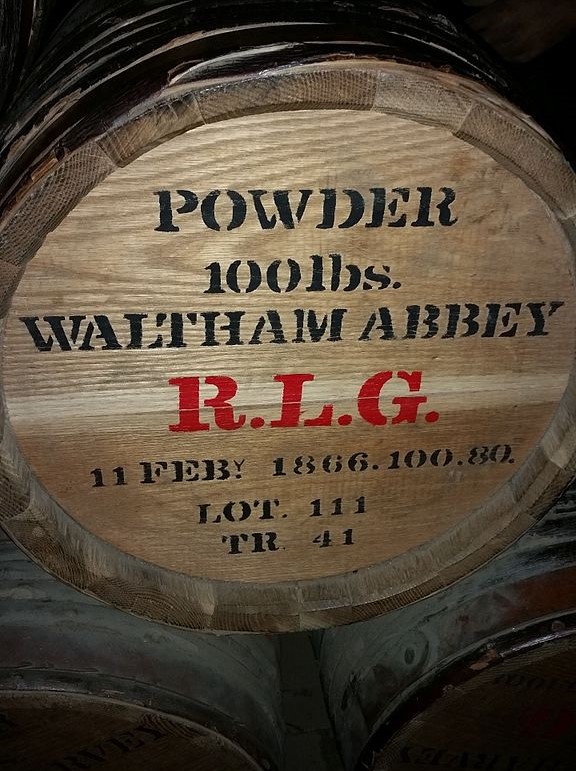
Black powder is a mix of saltpeter (potassium nitrate), sulfur and charcoal, and was discovered in China during the early 9th century. Early formulations were only useful for fireworks and incendiaries, but by the 13th century, the knowledge had spread across Eurasia and the recipe had been improved to the point that cannons as we know them today were practical. The saltpeter is the largest ingredient by weight, and provides oxygen, allowing combustion of the other two components to occur much more rapidly than would otherwise be possible. Charcoal is the main fuel, while the sulfur lowers the ignition temperature of the mixture, improving reliability. When they burn together, about 43% of the mass becomes gas, while the rest remains solid. Most of this leaves the gun as thick smoke, but some remains behind to foul the weapon.
Early gunpowder simply consisted of the three ingredients being mashed up in a mortar and pestle for a long period. This made things extremely hazardous, and the "serpentine" powder produced also tended to separate during handling, spoiling efficiency. Mixing it again in the field would solve this, but it raised issues of its own, most notably a highly explosive dust. A solution was eventually found during the 15th century in the form of corning, where the ingredients were mixed wet, and then formed into grains of a specific size to dry. Each grain contained all three components, preventing them from separating. This also made the powder much more effective, as the grains ignited much more readily and reliably than serpentine powder did.2
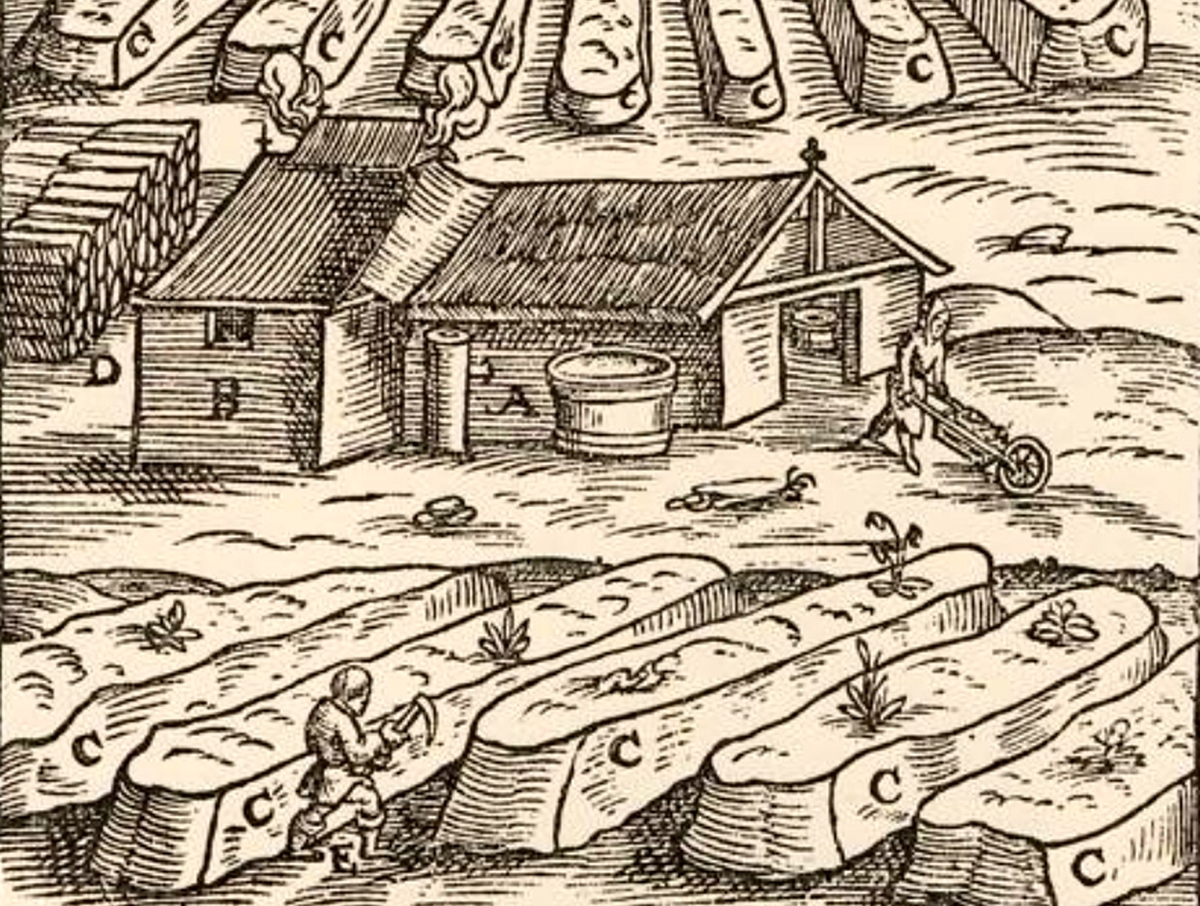
A Saltpeter production facility
Charcoal was the easiest ingredient to come by, as it was a major ingredient in metal production. The usual technique was to create a cone of sticks and cover it with earth, then set it on fire. Different wood was used for different types of powder. Willow was preferred for heavy guns, hazel twigs for handheld weapons. Sulfur was also fairly easy to get. Although it's found in only a few places in Europe, the quantities needed were small enough that it wasn't a huge issue. That just left saltpeter. Saltpeter does occur naturally in some places, but it can also be made artificially, a necessity in many countries including England.3 There were two ways to do this. One was to find existing niter-rich earth (old cesspits were a good place to look) and then extract the saltpeter by mixing the earth with wood ash and running water through it, then boiling the water. The second way is to generate the earth artificially, by mixing earth with horse dung, lime, and lots of urine, then letting it sit for a few months before refining it.4 Improvements in refining technique that removed highly hygroscopic5 sodium nitrate during the 16th century contributed to the longevity of gunpowder.
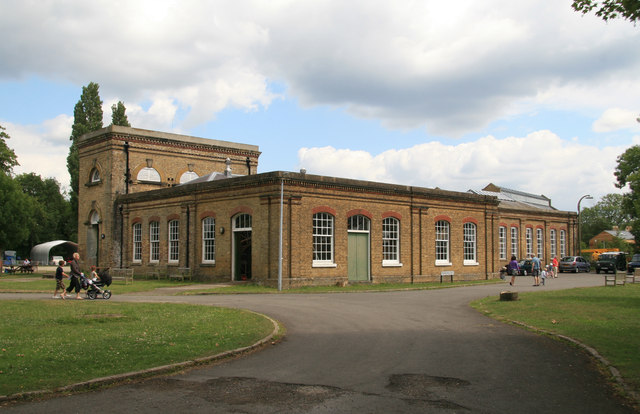
Waltham Abbey
Gunpowder development stagnated until the late 18th century, when the British began to manufacture most of their powder at Waltham Abbey, under the direction of William Congreve.6 Congreve pushed for experimental work, and for improvements to manufacture, everything from sorting powder by size for different applications to improved mills and presses. The biggest innovation came during the 1790s, when "cylinder powder" was introduced. This used a new method for making the charcoal, heating it in sealed iron canisters. This charcoal allowed charges in most British guns to be reduced by a third, a major financial and logistical advantage. Improvements were also made to the proof methods used to test powder before it was accepted for service. Various devices were used, the most successful of which was a simple mortar loaded with a measured charge of a new batch of powder, with the results determined by how far down the proof range the ball landed.

Powder development stagnated throughout the first half of the 19th century, but the growth of guns, both afloat and ashore, started to drive further innovation. In 1839, the whole thing was placed on a theoretical basis by French scientist Guillaume Piobert, who figured out how the combustion process worked. Unfortunately, the explanation is quite long and complicated, so we'll pick up with it next time.
1 Liquid propellants have been proposed for guns, but they've never worked very well, certainly not to the point of being deployed at sea. ⇑
2 This is because the flame required to ignite each grain can pass through the gaps between the grains of powder, while the denser serpentine powder blocks it from getting through. ⇑
3 This isn't a mistake. My main source on this is the book Dangerous Energy, about gunpowder manufacture in England. ⇑
4 I'd be remiss if I didn't mention the Confederate Nitre and Mining Bureau, who were tasked with securing saltpeter for their doomed war effort, and asked everyone to save the contents of their chamber pots. ⇑
5 Meaning essentially water-attracting, as in it pulled water out of the air. ⇑
6 This isn't the Congreve responsible for the Congreve Rocket. That was invented by his son. ⇑
Comments
That's interesting. I'd have thought that, for the purposes of making charcoal, any wood is as good as any other.
@bean "...pretty much all solid propellants for guns are known as powder."
Even the weird cordite noodle-things are called powder?
More or less. If I was writing about a cordite gun, I wouldn't hesitate to talk about the "powder charge".
@quanticle
So would I, but my source on this is pretty clear. Doesn't say why, though.
The charcoaling process preserves the micro-structure of the wood. So, an airy porous wood becomes an airy porous charcoal etc. This would factor into things like particle size, shape, strength, crush resistance... Hypothetically charcoals from different woods would inherit different mineral compositions as well, but I have a hard time imagining it making a difference.
I would be curious if late period black powder was made from coke instead given England's well known wood shortage.
Charcoal burning is actually very skilled labor. There is only a very fine line between allowing enough air to char it all the way through and adding so much that the whole charge burns to ash.
My aunt was a big genealogy kick a while back. Apparently, my forefathers were charcoal burners in 18th cent Luxenberg.
I heard once, though no idea of the source, that the Confederates started the war without a single powder manufactory, and by mid-war had built the largest one on the continent.
Incredible when you think of how much progress was made long before anyone invented this whole science thing. Early gunpowder is something I'd love to really dig into the history of, because it's at the nexus of econ history, growth of state capacity, and explosions.
I was intrigued with the idea that charcoal made in iron cylinders would reduce the required charge by 1/3. ie. 50% more effect per mass.
Which is stunning. Imagine having one change that gave all the engines in your military a 33% fuel efficiency improvement.
A brief search found one person who actually discussed why. And he was writing in 1832 so it wasn't backed up by actual scientific measurements.
https://books.google.com.au/books?id=6ifVymz576gC&pg=PA16&lpg=PA16&dq=gunpowder+%22cylinder+powder%22&source=bl&ots=O0xXZXSJgB&sig=ACfU3U0wIvlNSIgFHfieqy4Ik7tWC18MA&hl=en&sa=X&rediresc=y#v=onepage&q=gunpowder%20%22cylinder%20powder%22&f=false
His theory, which ISN'T insane by modern standards, is: In normal charcoal the volatiles driven off from the wood are combusted in place, then the ashes from this combustion end up contaminating the charcoal. Whereas the charcoal made in sealed distilling chambers drove away all the volatiles and removed them cleanly from the remaining charcoal.
Something to keep in mind next time you are accidentally sent back in time and need to ingratiate yourself with the local ruler.
@bobbert
Interesting. That makes sense, but it's also something I didn't think much about.
@echo
The only book I know of that covers that stuff was also the primary source for this post. The title is Dangerous Energy, and while it's primarily focused on the archeology of gunpowder manufacture in England and Wales, it also covers a lot of that stuff incidentally. A lot less useful on smokeless powder, but I had other sources for that.
@Doctorpat
Unfortunately, Dangerous Energy doesn't talk about the reasons it works.
A couple additional interesting facts: - DuPont got their start in powder manufacture.
- Powder manufacture is hazardous, particularly the grinding steps. It is, after all, applying energy to an explosive. There was a lot of emphasis on non-sparking materials, following procedures, and so on. Also - at least at DuPont, the manufacturing area was deliberately set next to a river, in a row of almost-bunkers - except with very light roofs and a very light wall facing the river. The idea is to minimize an explosion to only one bay rather than the whole site.
Re: Cylinder Powder My guess is that the process is able to reach higher temperatures and drive off the last of the volatiles (heavy tars and such).
Such charcoal would be expected to burn with a much hotter flame. I agree that the 50% improvement in explosive power is very impressive.
@bobbert: While cordite is often referred to as "powder" in some contexts, those "noodle-things" were the "cords" that gave it its name.
@echo: They were shockingly poorly supplied. I don't know about powder (though I recall hearing that there were only two mills in North America during the Revolutionary War), but I do know that they only had a single facility for making guns of any size, and even that only came to them when Virginia joined the CSA after Fort Sumter. One of these should be the right link: Tredegar Iron Works or (Tredegar Iron Works)[https://en.wikipedia.org/wiki/TredegarIronWorks]
18th-century France had state-owned gunpowder manufacturing- in the period immediately before the Revolution, its superintendent was a certain Antoine Lavoisier.
The state gunpowder factories produced a range of grades of gunpowder. As well as the highest grade reserved for the military, there were grades for hunting, commerce and mining. The lowest grade was poudre de traite, "trading gunpowder", which was sold to French slave traders who traded it for slaves.
During the Revolution (which Lavoisier sympathised with), he ordered a shipment of this poudre de traite to be moved out of the Paris Arsenal to make room for higher grade gunpowder. Some revolutionaries who noticed the powder being shipped out feared that Lavoisier (whom they didn't trust) was moving it out of Paris to make the city defenseless against the king's armies. His attempts to explain his actions were not helped by the fact that the revolutionaries misread the labels on the powder as poudre de traitre, or "traitors' gunpowder"!