Corrosion is a serious concern in the maritime environment. A mix of salt, water and air is about the worst possible environment for metal objects to survive in, and if corrosion isn't dealt with, usually at significant expense, it rapidly becomes a safety issue.
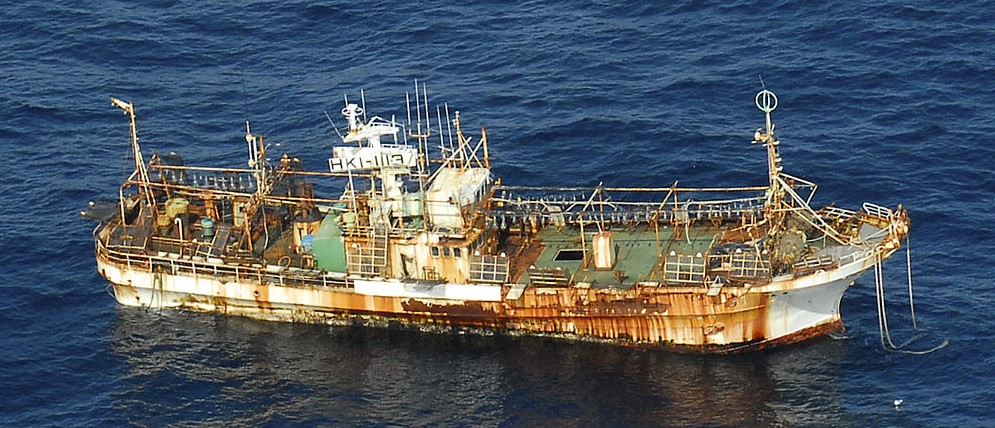
Marine corrosion is electrochemical in nature. For various reasons, different portions of a metal will have different electrical potential, causing electrons to flow between them. Areas with extra electrons (known as cathodic areas) give them up to the sea, combining with water and dissolved oxygen to produce hydroxyl ions (OH-). These are then drawn back to the areas which gave up their electrons, known as anodes, where they combine with the atoms of metal to form metal oxides. If the ship is primarily made of iron or steel, the product is hydrated iron oxide, more commonly known as rust. Rust is generally quite fragile, and doesn't protect the underlying surface very well. Other metals, such as aluminum and stainless steel, also corrode, but the products of said corrosion instead cling tightly to the surface, protecting the underlying metal from further corrosion. In fact, you may know aluminum rust by another name, sapphire.
All of the various forms of marine corrosion are driven by this basic process, although the ways in which the electrochemial potential difference occurs vary widely. The simplest is galvanic corrosion, which takes place when two dissimilar metals are in contact. Each alloy has a different inherent electrochemical potential, with stainless steel, copper and bronze being quite cathodic, normal steels in the middle, and aluminum and zinc being the most anodic. Galvanic corrosion can be a serious problem if multiple metals are used on the outside of a ship, such as corrosion-resistant bronze propellers, which will eat the steel around them. But the galvanic series offers a simple solution. Fit pieces of a metal that is more anodic than the one you want to protect, and they'll corrode first. Replace these "sacrifical anodes", traditionally made of zinc, occasionally, and the problem is solved.
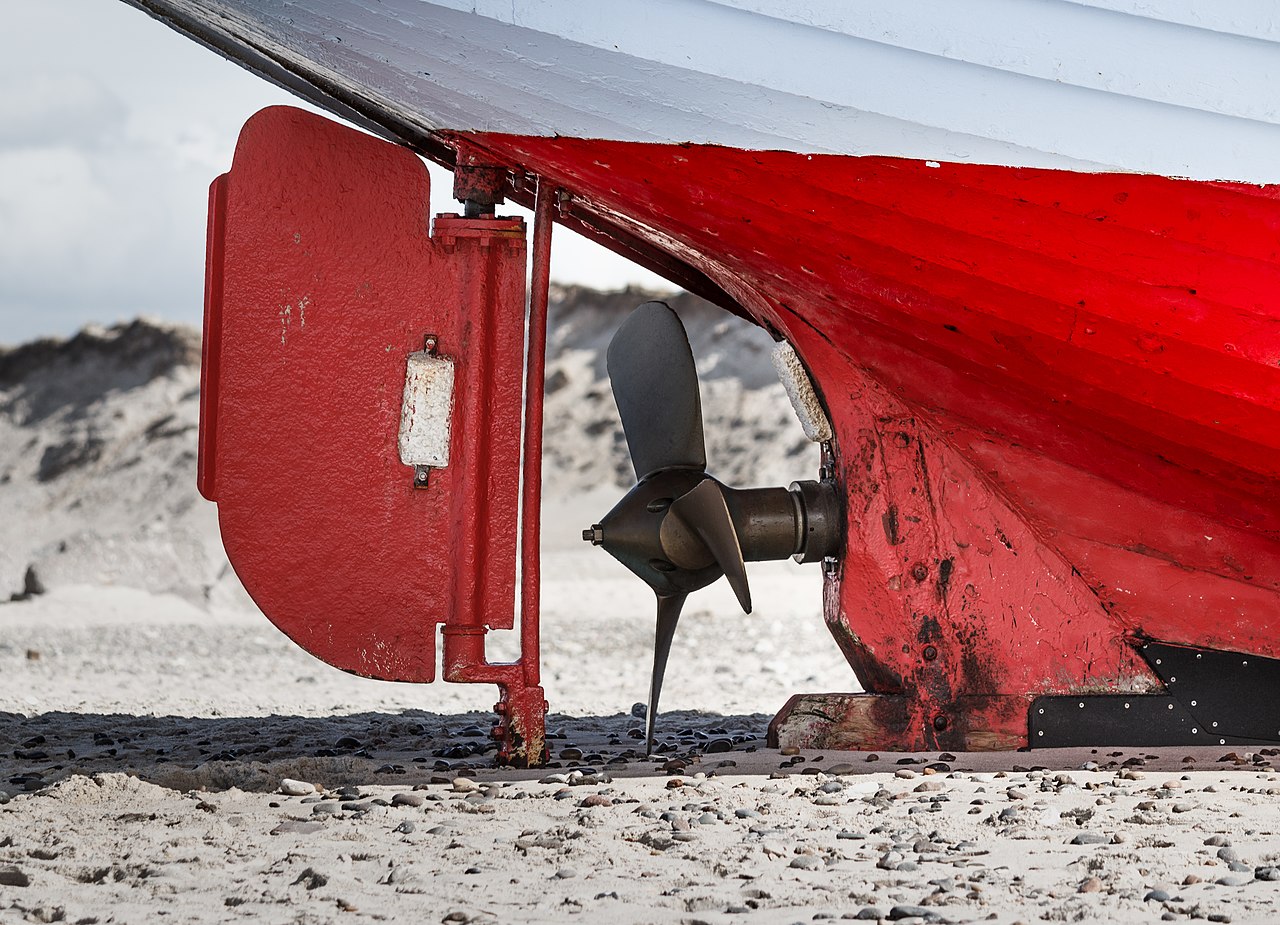
Sacrificial anodes on a small boat
But how does a piece of iron left all by itself rust? The answer is that while dissimilar metals are the easiest way to generate the potential differences that drive corrosion, they aren't the only way. For bulk metal, the process is dominated by tiny potential differences between the crystals that make up the metal's grain structure, each of which has its own orientation and faults, and each of which will have very slightly different potential. In the presence of an electrolyte, even an imperceptible film of water pulled out of the air by salt left on the surface, that's enough. Other mechanisms can drive this process even faster. Oxygen depletion in a crevice can produce potential differences, as can stress on the metal, a major factor in aircraft corrosion. And immersion in water or the effects of welding can break down the passivation layer on stainless steel or aluminum, leading to the possibility of bulk material damage. And any induced current in the hull, such as from an electrical fault or even a nearby radar, can make things much worse.
Rates of corrosion vary widely. Steel in still water corrodes at about 125 micrometers per year, with the rate decreasing over time, reaching about 60 micrometers/year after 16 years. Moving water greatly increases the rate, to a maximum of about 1 mm/yr at a velocity of 12 kts, as can high temperatures, with 20-30% more material lost for every 10°C rise. Lots of oxygen also hastens things, either if the material is just above the waterline in the presence of air, or if it's just below, where the water is heavily oxygenated. Other factors can play a part, with certain bacteria causing heavy corrosion in the absence of oxygen, and calcium and magnesium in the water being deposited as a protective film.
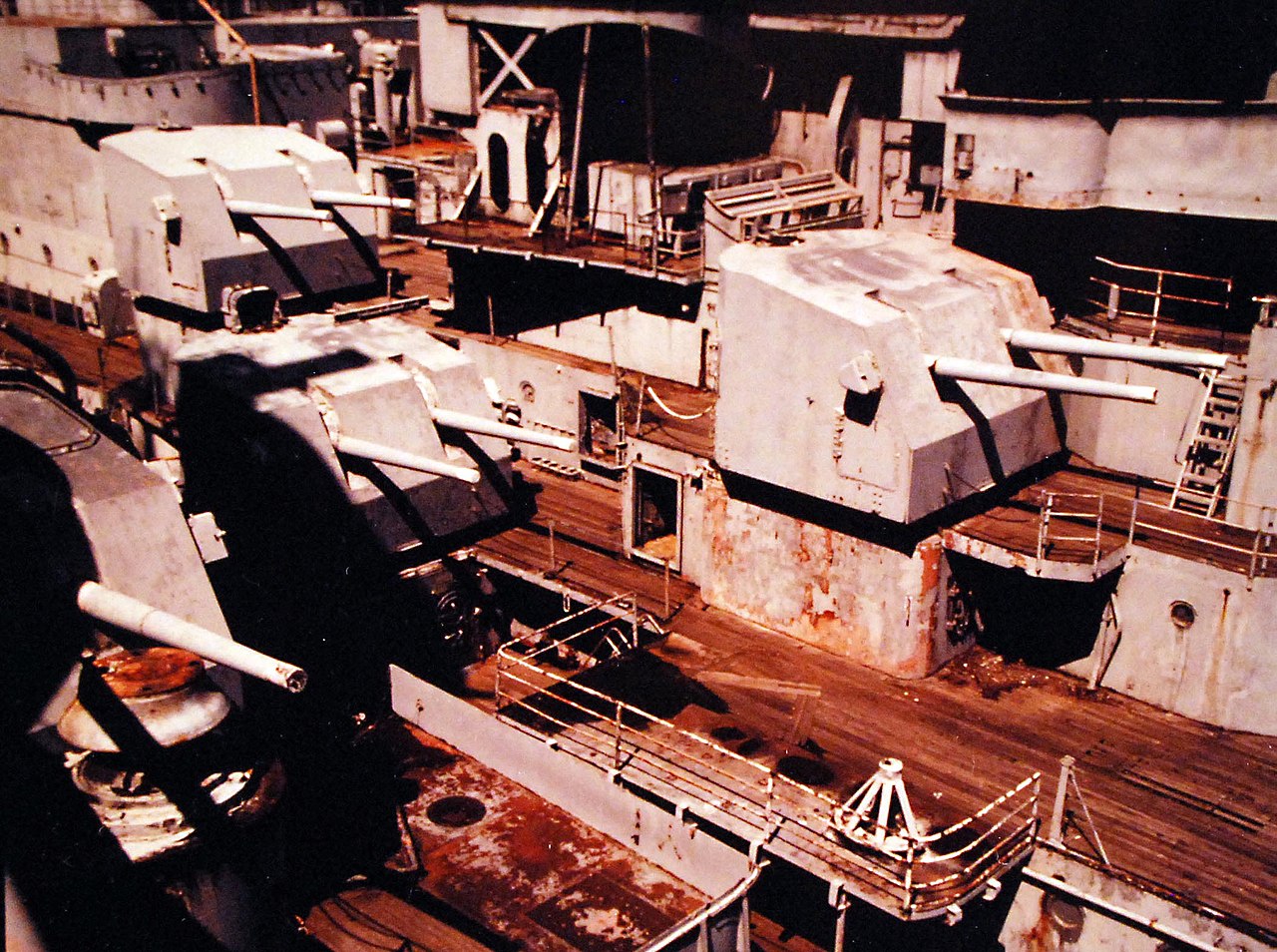
Corrosion can have effects besides the obvious structural ones. Bolts and mechanical systems can seize up, and corrosion can have surprising effects on electrical equipment. Earthing can be interrupted, while circuit boards can get extra traces. A particular problem comes from the formation of non-linear junctions on the outside of the ship, either in the antenna systems themselves or in areas like guardrails. These can produce harmonics, re-radiating signals and interfering with radio and radar systems. And not all corrosion comes from the sea, either. The most difficult areas to protect are actually inside the ship, in the machinery bilges, where a combination of salt water, oil, and high temperatures produce a fantastically corrosive environment. Eventually, zinc sprays and special epoxy paints solved this, but older ships often had to have structural members replaced due to corrosion damage.
Protection against corrosion is provided by a number of methods. Good design avoids or greatly mitigates crevice and bimetallic corrosion. The first line of defense against other types of corrosion is coatings, mostly paint, which straightforwardly isolate the metal from the water, stopping corrosion completely. Before and during WWII, ships used oil-based paints, which were cheap and easy to apply, but were also highly flammable and had to be reapplied frequently. Starting in the 60s, specialized primers were applied as soon as the plates were formed, which greatly reduced corrosion. Of the ships sent south in the Falklands War, only Hermes, built before such techniques were introduced, suffered serious corrosion.
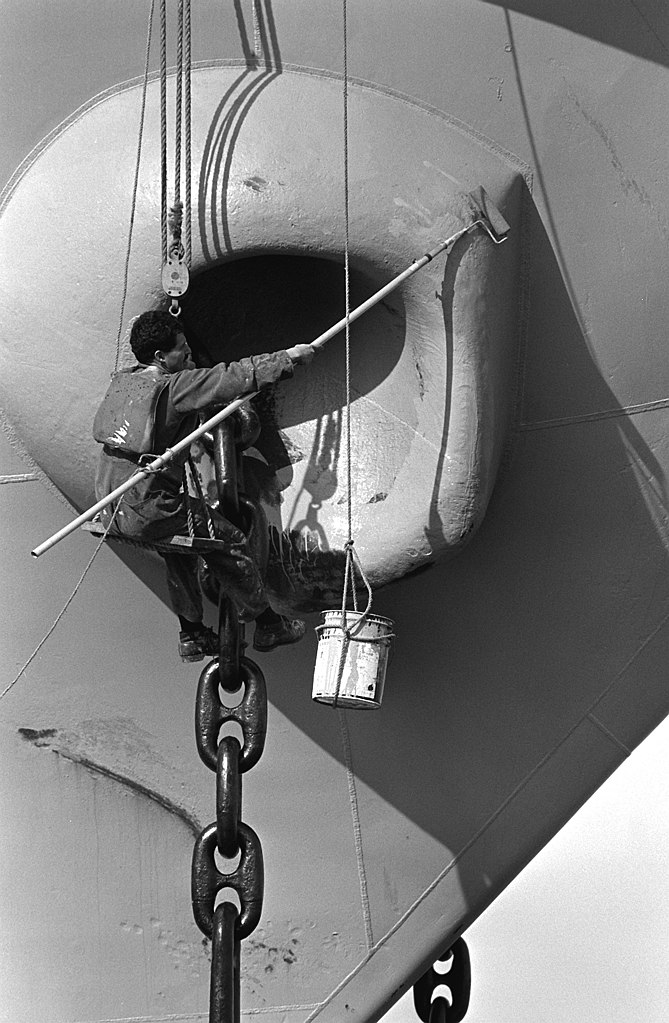
But paint can't cover everything, so other methods are needed to protect the exposed areas. The oldest is the sacrificial anodes mentioned above, which have the advantage of being simple and entirely passive, but also are fairly large and require regular replacement. Zinc is standard, although aluminum and magnesium can also be used. These metals do bring the danger of over-protection, which can lead to alkaline attack that damages the paint, and the production of hydrogen, with all of the dangers that implies. Modern ships instead use impressed current protection, where the entire hull is given a very slight (less than 1 V) charge, relative to a set of very small hull anodes made of a quite cathodic metal. The result is that the entire hull is very cathodic, and virtually no corrosion happens. The downside of these systems is that they're expensive to install and require power, but they are generally more effective than sacrificial anodes.
Corrosion will be a problem so long as man goes to sea, although modern methods have done a great deal to reduce its cost. Before the mid-20th century, it was common for ships in major overhauls to need hull plates replaced thanks to corrosion, but today, such work is rare, allowing ships to spend less time in dockyard hands and more time at sea, as well as allowing crews to spend less time painting and more time on other tasks.
For a somewhat more detailed look at this issue, I recommend Battle with Barnacles, an Indian publication that is a lot more fun to read than you would expect.
Comments
Thank you for covering this Bean. Most informative.
Have there been any problems with mating composite materials to metals? Not sure if I am asking this the right way as composites shouldnt/don't corrode, but I am thinking of the metals to which they are joined or overlay. Are modern naval vessels even using composites to a significant extent?
Your mention of the flammable oil paint reminds me of something. I seem to remember reading things like 'in preparation for war, her paint was stripped off and reapplied, and in some locations it was found that there were 80 coats'. I'm guessing that's because a little crack in the paint corrodes, so they figured it was better to just apply a new coat regularly rather than inspect to see if it was needed?
@Neal
I know you suggested this a while ago, and it was basically waiting until I happened across the right source. Can't speak to the composite issue, because neither that nor the other book I used are recent enough to have opinions. In general, I don't see any reason it would be a problem.
@David W
AIUI, most of that was because the people in question wanted their ship to look good, so they painted a lot. The amount of paint required to manage corrosion is generally less than that required to keep a ship looking really nice, and when it's an old warship with a big crew, throwing another coat of paint on will keep them busy, too.
Composites ought to be a major problem from a galvanic corrosion perspective - the electric potential difference between them and metals is almost battery-like when compared to typical metal-metal potential differences. Luckily galvanic corrosion is relatively easy to solve w/ coatings/zincs/strange incantations so it can be kept to the level of merely concerning, but it does make the metal parts of things get eaten up faster, and it sometimes shows up (at least in the aerospace world) as a major problem on the electrical side because of the funny things the electric potential of the composite/metal interface variably does to your "common" ground plane, which messes all sorts of electrical things up if you aren't careful.
Carbon fibre is electrically conductive and is nicely cathodic relative to say aluminium, so a carbon fibre and aluminium structure is subject to galvanic corrosion if it is wet for any length of time. It is often assumed that just making sure that the carbon fibres are safely coated in resin should stop this, but:
As a general rule for consumer products at least, you want a layer of old fashioned fibreglass between metal and the carbon fibre anywhere that it could be wet.
https://www.corrosionpedia.com/galvanic-corrosion-of-metals-connected-to-carbon-fiber-reinforced-polymers/2/1556
Galvanic protection, especially the impressed current type, is so effective and so cheap (compared to say painting and maintaining the painting on anything sufficiently large) that it is considered a real pity that it only works where you are immersed in water. You can't do it on a car for example, because little patches of water will not be in contact with the electric fields you are trying to establish.
It's convenient that impressed current systems DO work underground, where moist soil is enough that significant parts of modern infrastructure are protected for a couple of dollars worth of electricity.
The closest you can get to galvanic protection on a mostly dry structure is zinc coating. Which is why that's so common.
Doctorpat:
Didn't seem to stop car dealers offering it.
Well, there goes my evening.
Thank you Ryan and Doctorpat. That jogs my memory on the electrical issue. In 777 school in the late 90s I remember a Boeing engineer talking about that but it went past us as everyone was asking about drilling through composites, mating them, etc. It was all new back in that day.
Didn’t seem to stop car dealers offering it.
No. Strange that. : )
There is one thing that is applied to cars. Just because hooking a car up to a negative voltage source doesn't save it from rust, it's still a lot better than hooking it up to a positive voltage source. Which is why the car electrical system has the negative as grounded to the car body. Allegedly some early designs had the ground as positive, and that ended poorly. And quickly.
Is this similar to how using -48Vdc puts a positive charge on telecom gear to prevent corrosion? I'm completely ignorant of anything electrical.
Doctorpat:
It's been a problem at times even in the aerospace world; for instance, when early CRJ airliners found out that aluminium floor beams plus CFRP fittings (associated with the door frames, IIRC) plus passengers and crew tracking in road-salt-laced slush in wintertime equalled badly-corroded floor beams, requiring an expensive repair and retrofit program.