Even after a battleship's hull had been successfully launched, there was still a great deal of work to do to turn it into a fighting machine. Particularly in the early days of battleship construction, the hull at launch was pretty much just that. All of the other equipment necessary to turn it from a bare mass of steel into a fighting machine still had to be installed, tested, and made ready for sea.1
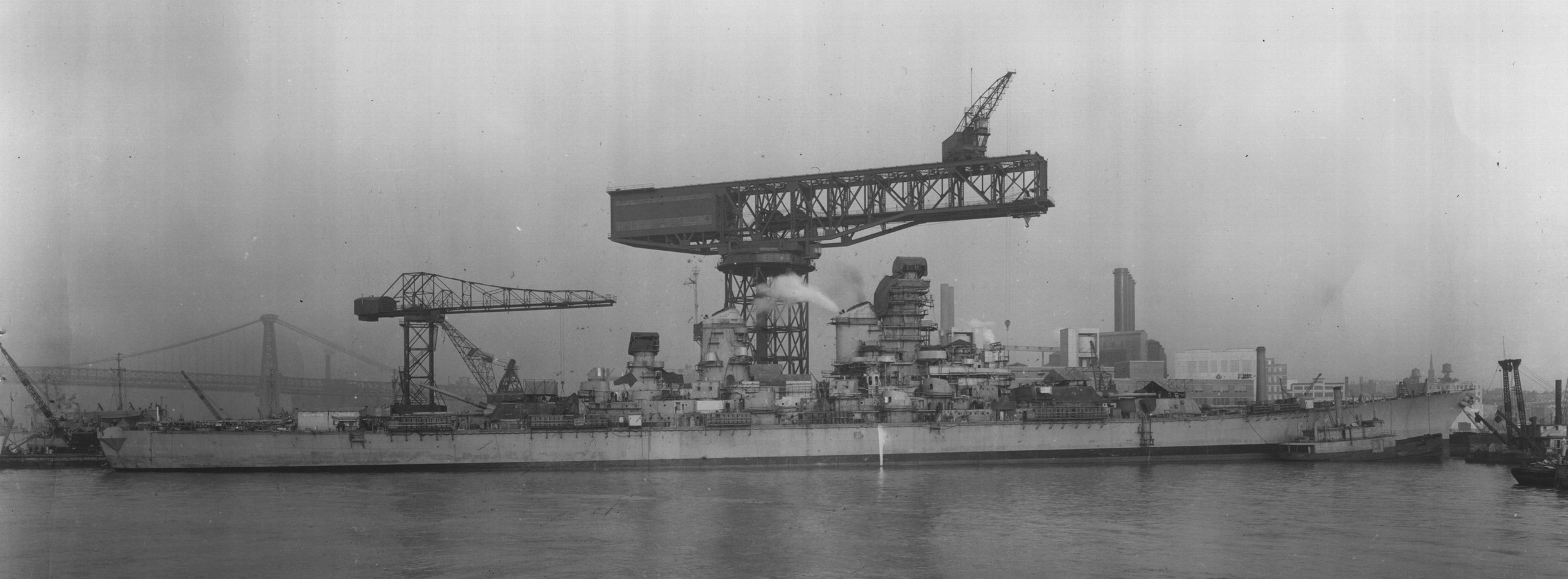
Iowa fitting out under the 350-ton crane at New York Navy Yard
This work would be done at a fitting-out dock near the shipyard, which had as its most prominent feature an extremely heavy crane to lift aboard things like boilers and turbines. These were passed through openings left in the deck and covered with bolted plates for strength during launch, then attached to their foundations. Through about 1900, sheerlegs, which were strong and simple, were used to shift loads aboard; these could only move loads directly out from the dock, which meant the ship had to be positioned very precisely. Later, enormous cantilever cranes were installed, some capable of lifting loads up to 350 tons and placing them anywhere within a 100' circle. These cranes were very expensive, and by leaving fitting of the heaviest components until the end of the construction process, the shipbuilders could economize on their use. Astonishingly, a few of these cranes remain in existence today, most notably the Titan Clydebank, having outlasted the ships they originally helped assemble.
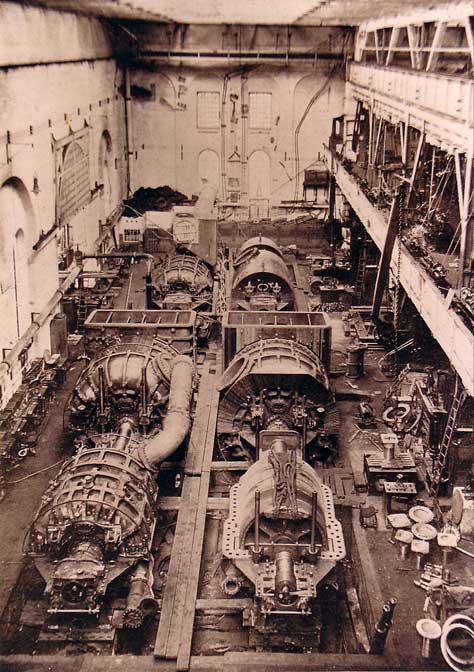
Turbines for HMS Bellerophon under construction
The machinery itself was usually bought from a specialist machinery builder, although some British shipbuilders had their own machinery works. This required a great deal of specialized equipment, everything from casting and forging to riveting and precision machining. Possibly the most difficult part, however, was cutting the gearing that connected the turbines to the shaft. This was done by hobbing, and the specialized machinery required to cut extremely large gears was often a bottleneck in warship construction. The British generally bid the machinery as a unit, while the Americans bought boilers and turbines from separate companies, which allowed them to take advantage of the knowledge gained in shore-based powerplants.
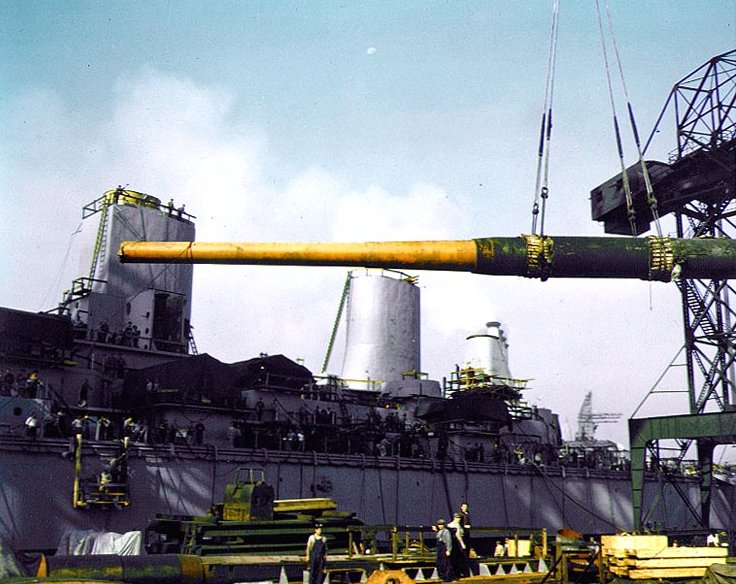
One of Iowa's guns is hoisted aboard. Note the ship's hull in the background.
The Americans procured their heavy guns exclusively from government sources, while the British made extensive use of the two massive ordnance companies, Vickers and Armstrong-Whitworth, later joined by Coventry Ordnance Works, in addition to the Royal Arsenal, Woolwich. Guns were among the most difficult objects on the ship to build, as they had to withstand the immense pressure of firing and be built to tolerances which would ensure accuracy at long range. Most British heavy guns used wire wound around the gun liner to provide the radial strength needed to resist the expansive stress of firing, but this allowed the gun to droop. The alternative was the all-steel gun, in which various sleeves were heated and then slipped over the liner and allowed to cool, locking them tightly together. This was initially heavier, although the disadvantage had gone by WWII.
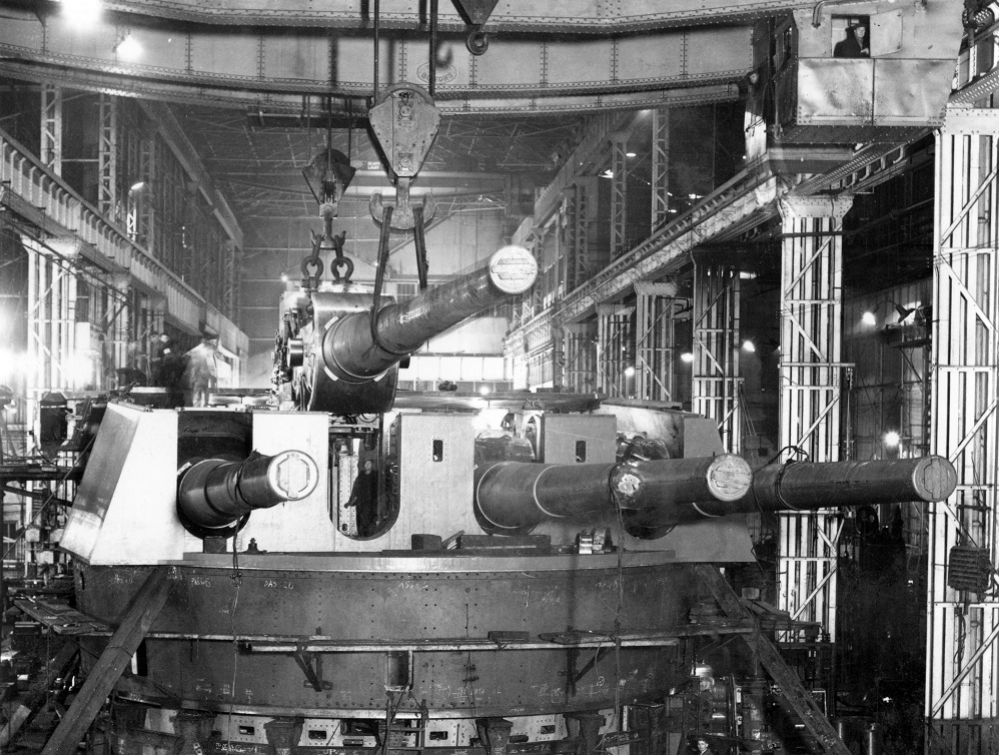
A quadruple turret for the King George V class being assembled at Elswick
The gun mountings, the heaviest components that had to be fitted, usually came from the same source as the guns themselves. They were much too heavy to be lifted aboard in one piece, with even the turrets of the earliest dreadnoughts weighing 450-500 tons, and those of the Iowas tipping the scales at 1,700 tons. Obviously, they would have to be lifted aboard in sections and assembled in place, but this was a risky situation, as correcting any problems afloat would be very difficult. To mitigate this risk, turrets were first erected ashore, in specialized gun pits. After everything was adjusted and working, which often took 9 to 12 months and made gun erection one of the major rate-limiting steps in battleship construction,2 the turrets were shipped off to be installed. If the gun pit was near the fitting-out berth, the parts might be shipped by the yard's railroad, but in many cases, they had to go via specialized barge to the shipyard. The heaviest part was usually the turntable, and it had to be placed very precisely on the roller path. The other components of the turret, everything from hydraulic machinery to guns and cradles to the armor, were hoisted aboard and hooked up.
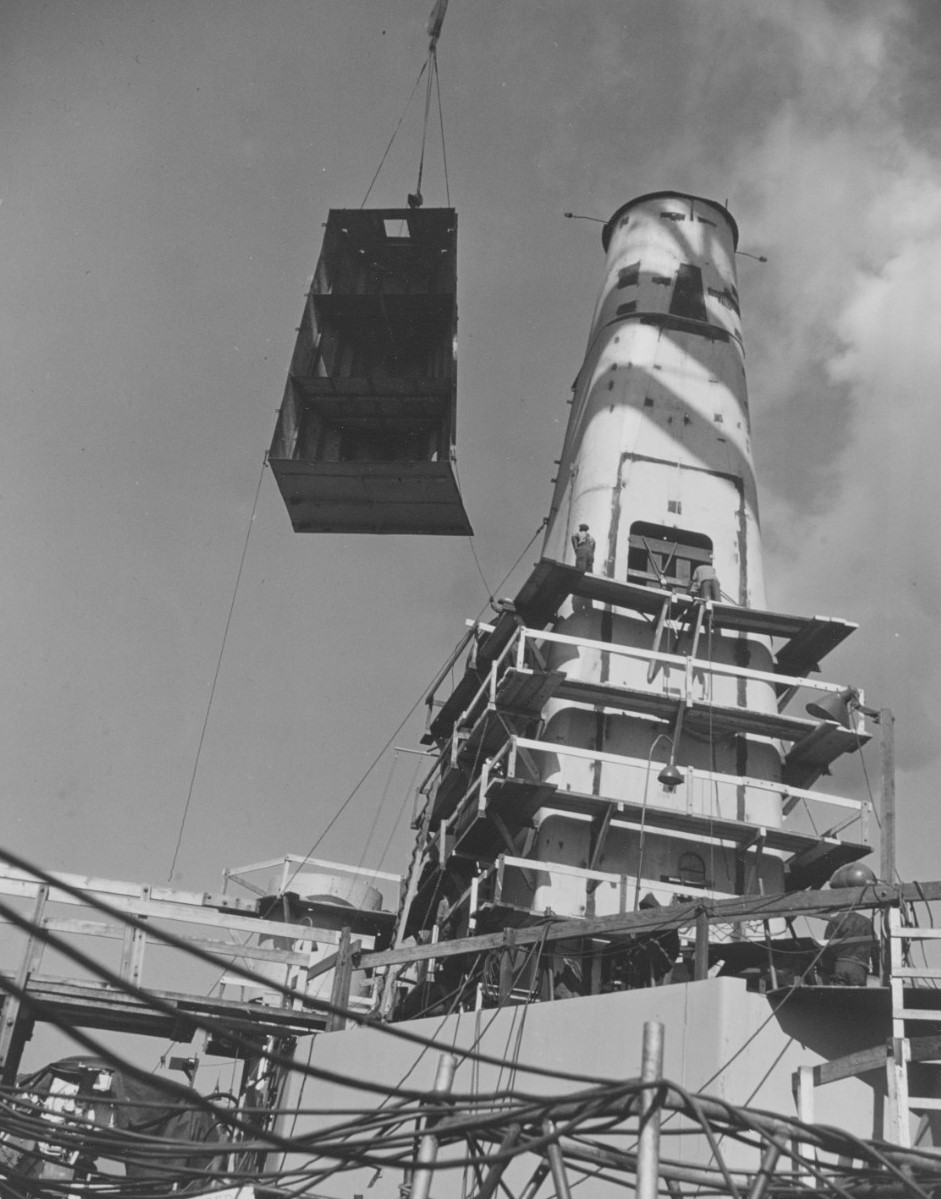
A section of Iowa's superstructure is lifted aboard
Of course, while the heavy stuff was the most obvious part of fitting out, it was very far from the only work that was done. Ships with external belts were often launched without their armor, which had to be bolted onto the backing. The superstructure, all of the stuff above the main deck, also had to be assembled. This process was much like the hull, although with slightly less attention to watertightness. The wooden deck would be laid down by the yard's shipfitters.
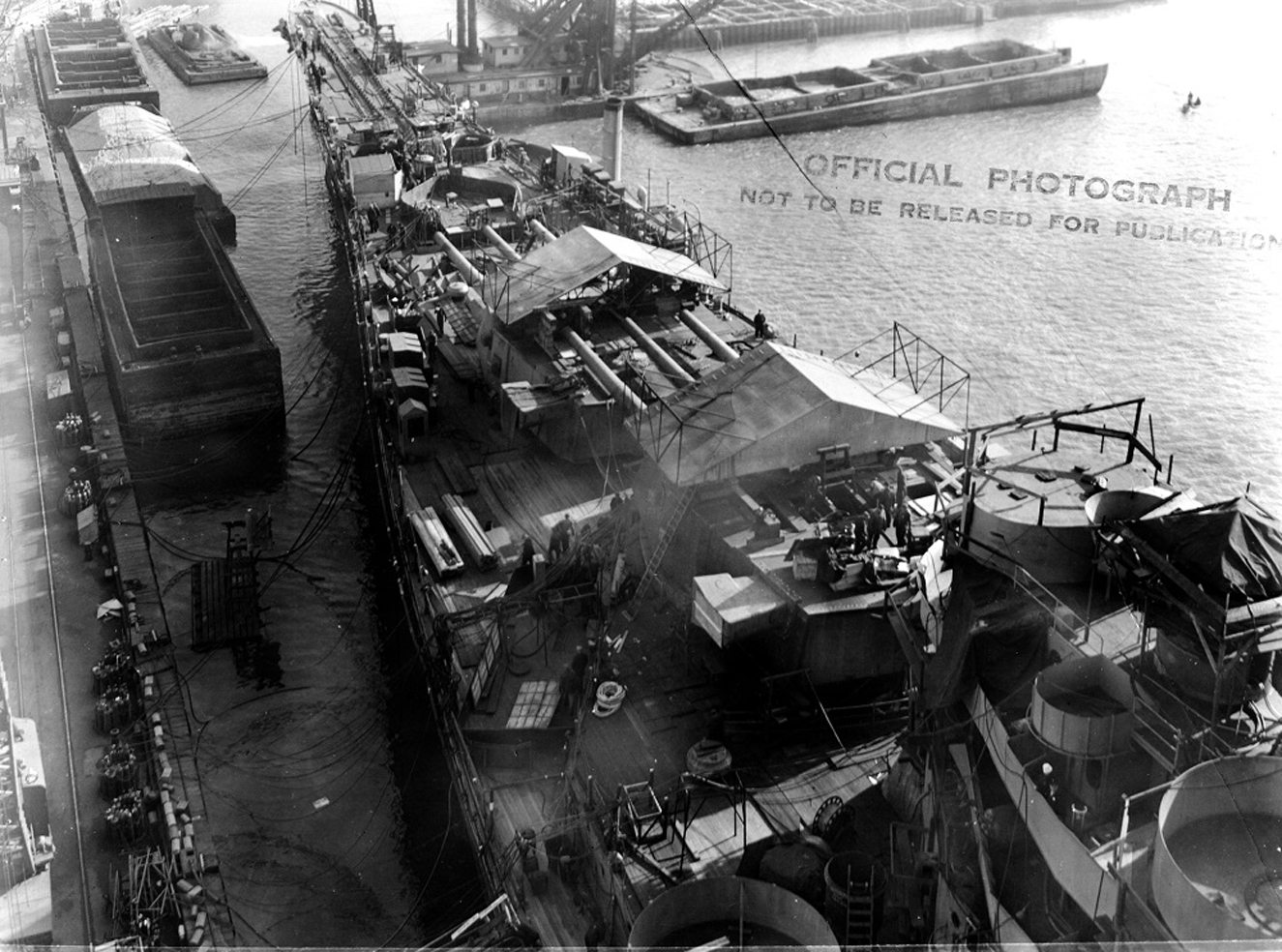
Iowa towards the end of fitting out
But a great deal of the work was done stuffing the ship with all of the bits that make a steel maze into a place where men could live, work and fight. Piping to carry water, waste, and hydraulic fluids. Ventilation ducting to make sure that they could breathe. Refrigeration equipment to keep the food and the magazines cool. Places for the crew to hang their hammocks. Galley equipment. Boat davits. Fire-control equipment. Urinal troughs and wash-basins. The contents of the sick bay. Miles of electrical wiring, carrying power and information throughout the ship.
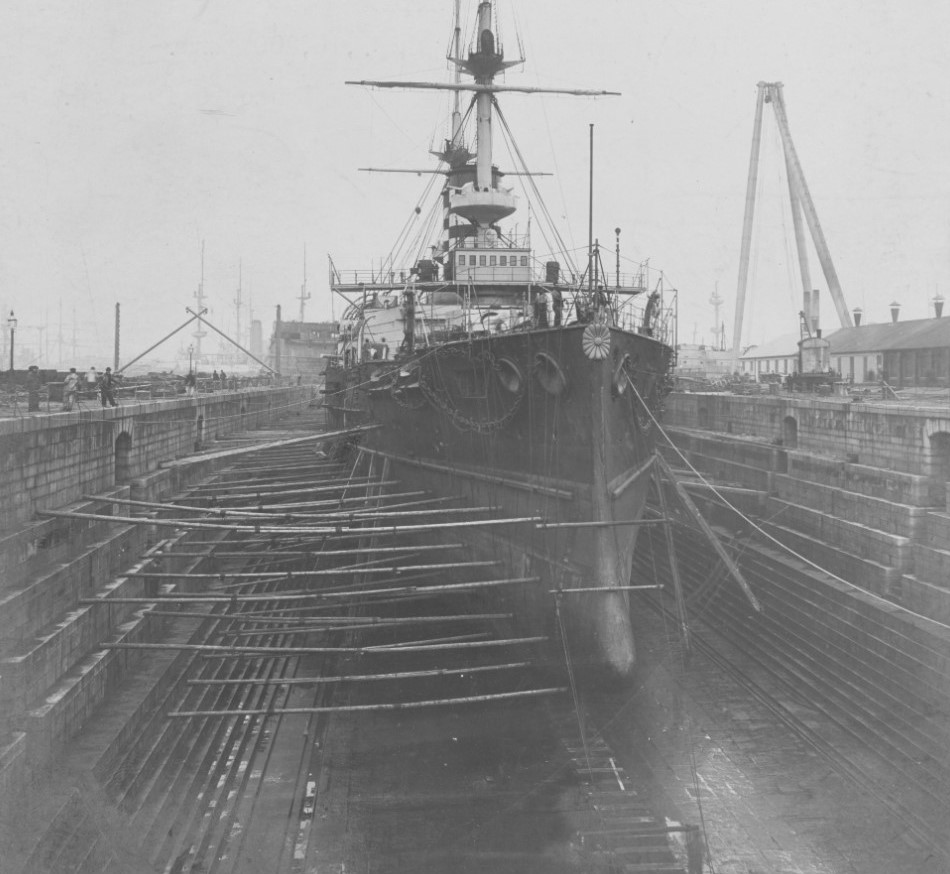
Mikasa in drydock for final fitting-out
Once the main fitting-out was done, the ship would be towed to a drydock. There, the cast manganese bronze propellers would be fitted to the shafts, the hull would be cleaned and painted with a fresh coat of anti-fouling paint, and the underwater fittings, such as torpedo tubes and seawater inlets for the machinery, would be completed.
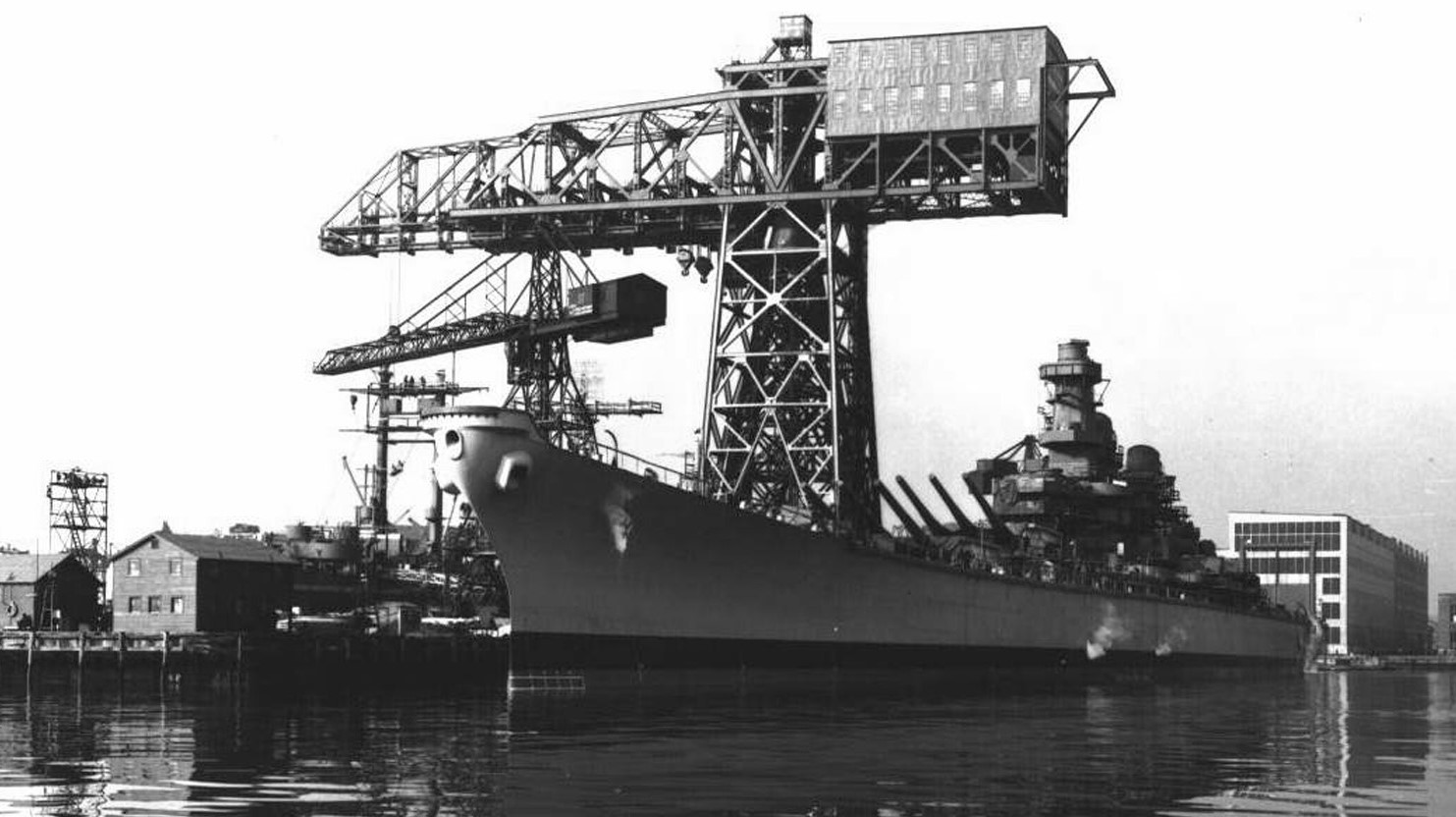
Wisconsin with the 350-ton hammerhead crane
When the nearly-completed battleship was floated out of the drydock, she would, in theory, be ready to enter service as the newest unit of her nation's navy. But theory and practice were a long way apart, and we'll discuss the means taken to close that gap next time.
1 There's been a definite trend in warship construction over the past century to install more and more equipment earlier in the construction process. The treaty battleships had things like engines installed before launch, reducing fitting-out time substantially. Modern warships take this a step further, assembling 100-ton modules that are essentially complete, down to such minutiae as bunks and fire-suppression systems, in giant workshops. These are then hoisted onto the slipway (which might be in a drydock) and post-launch fitting-out is kept down to the minimum possible. ⇑
2 This is true at least for British ships. The Americans appear to have found a way around this problem, although my sources on American warship construction don't give details. My best guess is that the relevant work for the USN was done by government-owned workshops instead of by private companies, which allowed the infrastructure to avoid the decay the British experienced. The US was also notably less reluctant to pump money into industrial expansion than the British. Unfortunately, while I have several excellent sources on British battleship construction, I have less on American battleships, and it shows in this post. If I don't give specific mention of American battleships, I'm probably talking about British practices c.1905-1920. Also, the Americans very much tended to build to their plans instead of using skilled workers to cover gaps in the plans, which could allow skipping the ashore assembly, probably one of the major rate-limiting steps. All that said, I have more than I did when I first wrote this, and will probably follow up with more detail in a separate post. ⇑
Comments
And how would this be different from civilian ship construction?
I'm assuming that with ULCC oil tankers, costing something like $100 million, don't need a year or two of fitting out after the hull is launched.
There's a couple of differences. First, keep in mind that the ULCC, at $100 million, costs something like 5% of what a Burke does, despite being ~10 times the displacement. Steel is cheap and air is free. But military systems aren't. So there's a lot less stuff that has to be crammed into the hull while it's fitting out. (The stuff for a civilian ship comes later and is called cargo.)
Second, modern construction methods are very different, and emphasize doing as much of the work as early as possible in the process. So the engine room was probably built in a building somewhere to the point where it's basically ready to go, then hoisted into the drydock. When the ship floats out, it's essentially ready to go.
The value for a civilian ship comes later and is called cargo.
I like that line. It crystalizes so many vague concepts.
It really does. Actually, let's do math on this. A T1 supertanker (the largest currently active) cost about $125 million in current dollars. It can carry 3,166,353 barrels of oil, and crude is currently at $63.14. So the total value of the oil aboard one is $199.9 million. It's more valuable than the vessel, but not hugely so. On the other hand, that's a crude carrier, and I expect the ratio might be different for a container ship. (Also much harder to analyze, so I won't bother.)
I think the ratio is similar for car carriers- the only costs I can find for one are "$100M plus" (unsourced) and $137-144 million (but that last is weird because it's a Jones Act-compliant ship which will dramatically increase the price, and is smaller than many car carriers in service).
A cargo of about 4000 new cars is probably worth a bit over $100M, depending somewhat on whether it's loaded with Hyundais or BMWs...
Interesting. I'd have guessed that cargo value/vessel value would be higher for car carriers than for tankers, because crude is fairly cheap. On the other hand, liquids are unusually easy cargoes to handle, while cars are unusually difficult, which is going to drive up the price of the vessel.
All that said, it turns out that you can find the average value of a TEU. It's obviously highly variable with the type of cargo, but the average seems to be in the range of $40k/TEU. A Maersk Triple-E costs $185 million and carries 18,340 TEU, for a total cargo value of $733.6 million. This is a lot more than the value of the ship, or the ratio for car carriers or crude, unless it's entirely loaded with wood and paper ($2.7k/TEU).
Though, arguably to compare a Maersk Triple-E to say an aircraft carrier, one should compare the value of the cargo carried over a 30 year lifespan, compared to the value of the carrier over that same lifespan (adjust number of years to match what the actual lifespans are).
But anyway, the point is made. Cargo ships appear unrealistically so much cheaper than military ships because the cost of the cargo ship is only a small fraction of the value of the total transport system they provide, whereas a military ship has the entire cost (less personnel and consumables) up front in the construction and fitout price tag.
Operating costs for a warship aren't exactly trivial. A Burke costs something like $44 million a year to run. But yes, the distribution of costs is very different. And I wouldn't describe cargo ships as "unrealistically cheap" either. Most of the cost of a modern warship is in the electronics, whereas the electronics on a civilian ship are some radios and a mass-produced navigation radar.
Why did they refrigerate the magazines? I know that you get variable burn rate/ballistics in small arms depending on powder temperature, so I assume that's what's going on, but what temperature did they target?
You're correct about the reasoning. It was a fairly serious problem for ships that mixed turrets and engines. The temperature varied between navies. The USN was an outlier on the high end, apparently keeping the magazine at 90 F. Navweps has info on range table temperatures, which should correspond to where they kept their magazines. The British used 80 F, while most other navies used 15 or 20 C.