One of the great battles of the Second World War was fought in the shipyards. Moving the products of American industry to where they were needed to support the war effort would take ships, and when the US entered the war, those were in short supply. The centerpiece of this effort was a new design of freighter, intended to be easy to build and operate, dubbed the Liberty Ship. Existing shipbuilding capacity was insufficient, and through several waves of expansion, US industry geared up to produce 24 million tons of shipping capacity throughout 1942-1943.1 Ultimately, they would produce 2,708 Liberty Ships, in addition to about 3,000 other vessels built for the Maritime Commission, the agency charged with supply merchant ships for the war effort.
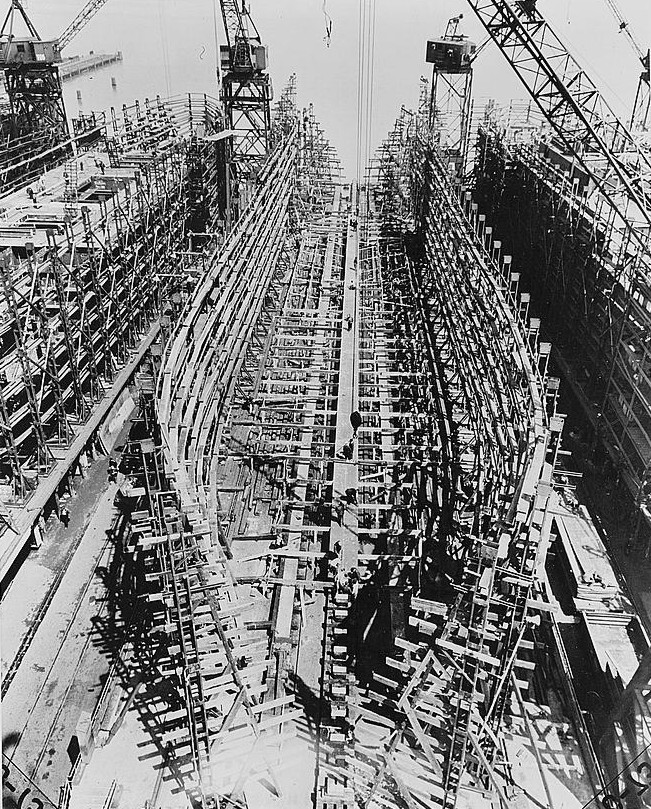
Day 2: Keel plates are welded on the slip at Bethlehem Steel's Fairfield yard
Building the vast fleet of Liberty Ships, by far the largest number of major seagoing vessels ever built to a single design, required a radically new approach to the problems of shipbuilding. Traditional methods relied on skilled labor and built high-quality vessels in small numbers. But the name of the game for the Liberties was multiple production, as builders raced to send ships down the ways as fast as possible, minimizing the time each had to remain on the slip before launch, as that was usually the bottleneck. From the first round2 of ships to the tenth in a given yard, average time on the ways fell by 80%. The overall victor in this contest was Oregon Shipbuilding, who managed to maintain a pace of 17 days per round in mid-1943. A few ships were built much faster as propaganda exercises, the record-holder being Robert E Peary at Richmond, launched 4 days, 15 hours and 29 minutes after her keel was laid, thanks to extensive prefabrication and massive use of resources. Three days later, she was completed and handed over to the Maritime Commission. But while this was a one-off, the average Liberty delivered in the last third of 1943 had had her keel laid only 41-42 days previously.
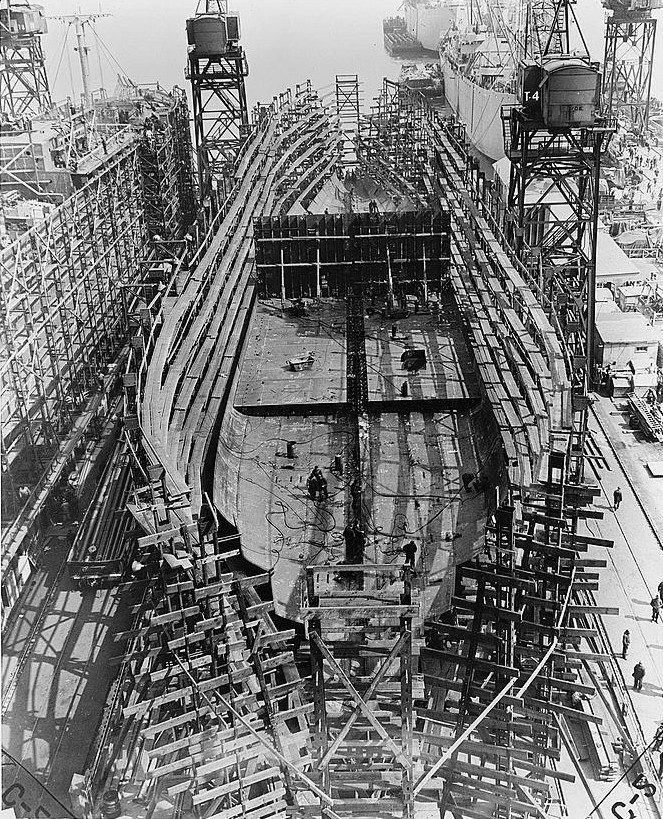
Day 3: The bottom and midships bulkhead are assembled
Prefabrication was one of the great innovations of the Liberty program, although not to the extent used for Peary. Traditionally, a shipyard would take in steel plate, shape it in its shops, and then do most of the assembly work on the ways, with individual pieces of steel being riveted into place as the ship grew. The Liberty shipyards also took in raw steel3 but did most of the assembly work off the ways, first making small modules in shops and then turning them into big ones, often weighing up to 45 tons, before hoisting them onto the growing ship. This let more men work on a given ship at once, and in far better conditions than an open slipway, and as a result, 80% or so of the steel for a Liberty was already assembled before the keel was laid. The vast scale of the program also let shipbuilders and subcontractors take advantage of standardization in ways not normally seen in shipbuilding, even if the standards of the auto and aircraft industries weren't reached. Suppliers of components could invest in tooling that would greatly cut cost, but only if used over hundreds of units. In the yards, workers could be trained for a small number of tasks and set to do them over and over, with all construction of a given component done in a dedicated shop or set of shops.
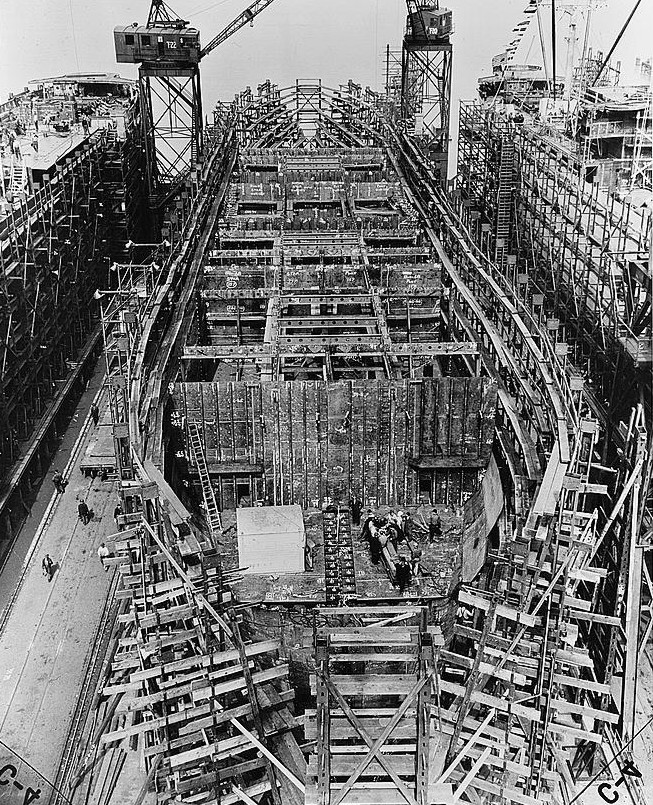
Day 6: Sides and bulkheads are erected
Another innovation that the Liberty program took advantage of was welding. Traditionally, ships had been riveted, which took a fair bit of skill, as well as requiring extra material to make up for the rivet holes. Welding was easier to teach to the men and women who had never built a ship before, and could be done faster. It also meant that the ships were lighter, but as with most new technologies, welding brought problems. Several ships suffered serious cracking, with two Libertys sinking after structural failure in heavy weather, and T2 tanker Schenectady breaking in half before her first voyage in calm weather. These were primarily a result of design flaws which encouraged cracks that could then propagate across welded joints, coupled with poor welding technique. Minor design tweaks essentially fixed the problem, although Kaiser's reputation suffered as his name was prominently linked to the cracks.4
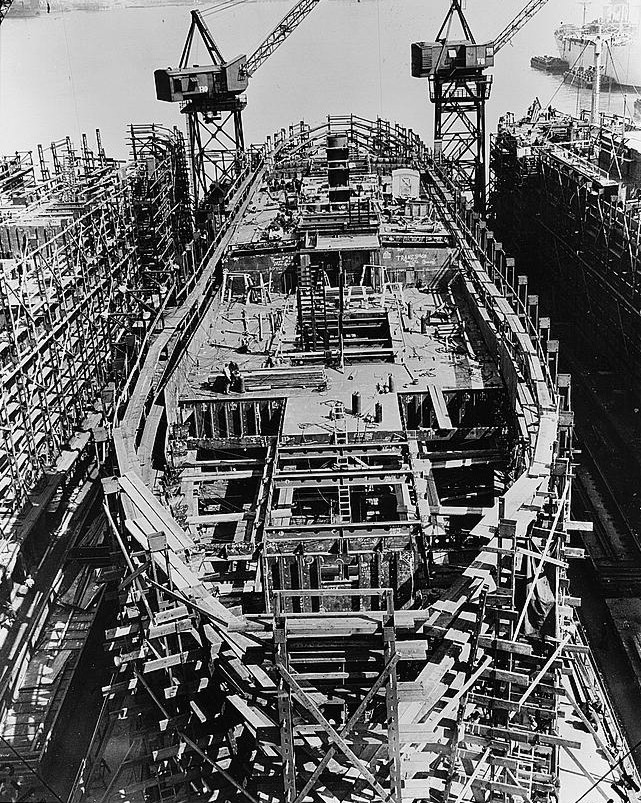
Day 10: Inner decks are installed
All of this work required a heavy investment in infrastructure, with a typical yard sprouting dozens of rolling cranes, extensive shops, and huge storage yards. In contrast to the mass yards of WWI, they were actually quite small, with much of the work being done well inland. But the result was astonishing, as throughout 1943, an average of 3.4 Liberty Ships were delivered every single day.5 Each took about 85 days from the beginning of assembly until delivery, with 35 days of fabrication, 40 days on the ways and 10 fitting out. 574,000 hours of labor went into this process, amounting to something like 750 men and women working 9-hour shifts for the duration of construction. Some yards did much better, the winner as usual being Oregon Ship, who brought labor requirements down to 352,000 hours.
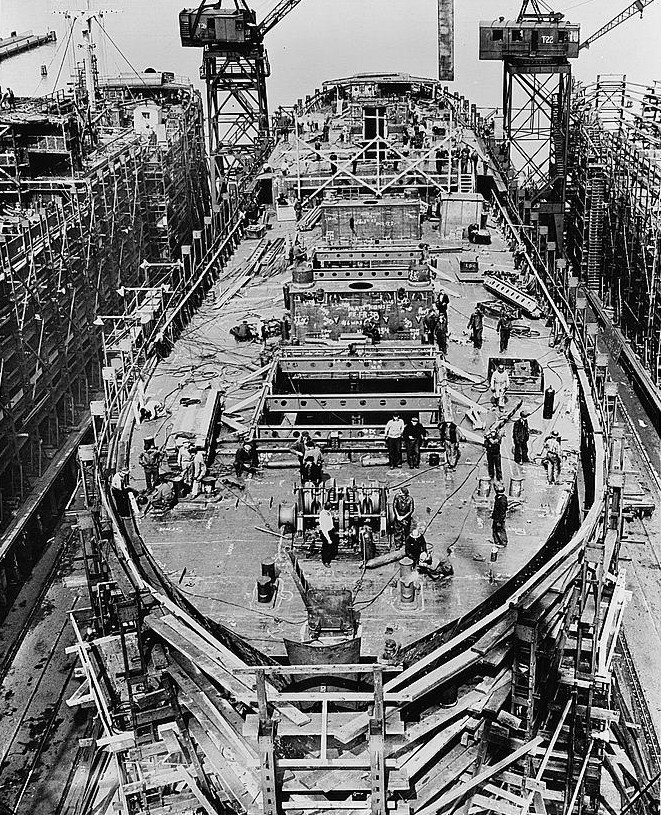
Day 14: Upper decks are in place
The vast majority of Liberty Ships were named after people, usually moderately famous Americans, selected by a committee of the Maritime Commission. All of these people were dead, with one inadvertent exception. Francis J O'Gara was named after the purser of a ship sunk by a submaine, who later turned up alive in a Japanese POW camp and became the only person to visit his Liberty Ship namesake.6 In an interesting and democratic twist, any organization or person that raised the $2 million in war bonds7 required to pay for the ship could propose a name, which was usually accepted, resulting in some rather obscure figures being commemorated, such as the founder of the 4-H movement in Kansas.
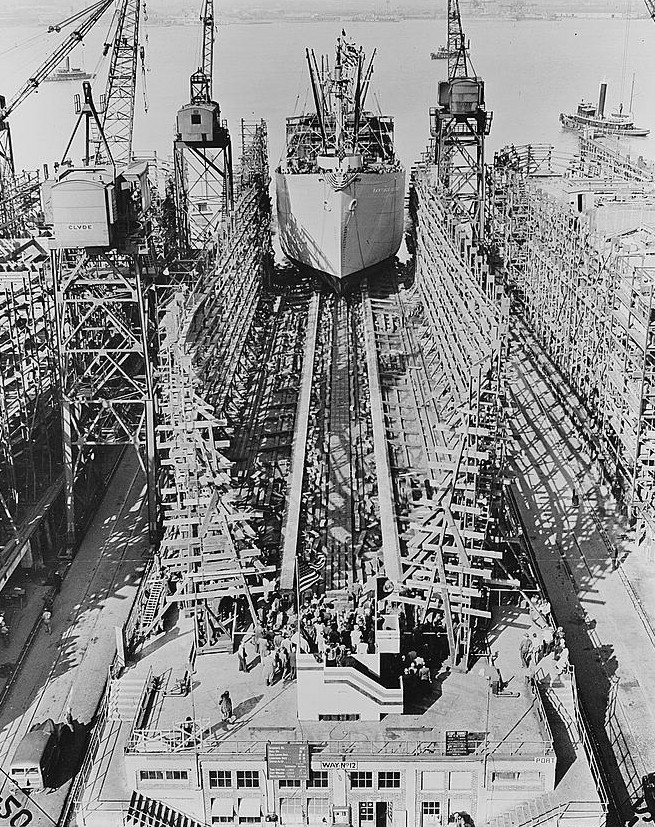
Day 24: The new Liberty Ship goes down the ways
The need to get hulls in the water pervaded the entire Liberty Ship program, from the most minor of details (ships often were completed and then sent straight to a repair yard to have things like doors ripped out and changed to avoid delaying the line) to the largest (200-ton deckhouses were fabricated separately and lifted aboard by four cranes working together). But the battle against the U-boats was one that the shipbuilders decisively won, alongside improved Allied ASW efforts, with construction exceeding losses every month from December 1942 onward. But even as the tonnage battle was won, plans were being drawn up for the replacement for the Liberty. But those ships wouldn't start to go down the ways until 1944, and even when they did, they never came close to matching the Liberty Ships in numbers. Next time, we'll turn our attention away from the production side and towards their operation.
1 Interestingly, the US as a whole produced only about 60% of its targets for this period as set in February 1942, but shipbuilding actually made its goals. ⇑
2 Essentially a complete batch of ships from all the ways of a yard. ⇑
3 At the beginning of the program there was talk of doing much of this work at specialist steel fabricators like bridge builders and shipping in modules whose size was set by transportation limits, but this didn't work out and they chose to fabricate on-site. ⇑
4 I intend to do a full post about this at some point, but going deeper into this is outside of my scope here. ⇑
5 This is equivalent in capacity (deadweight tonnage) to every large merchant ship built in the US in the whole of 1939 every 10 days. And that doesn't count non-Liberty ships, which were about half as much again. ⇑
6 This also makes it the only large American ship named after a living person that I am completely fine with. ⇑
7 Approximately $37 million in 2021 money. ⇑
Recent Comments