I've previously covered the development of naval steam propulsion systems, focusing on those used aboard battleships. But from the dawn of the 20th century, other systems were developed to push ships through the water, and today, variants of these systems dominate the marine propulsion landscape.1
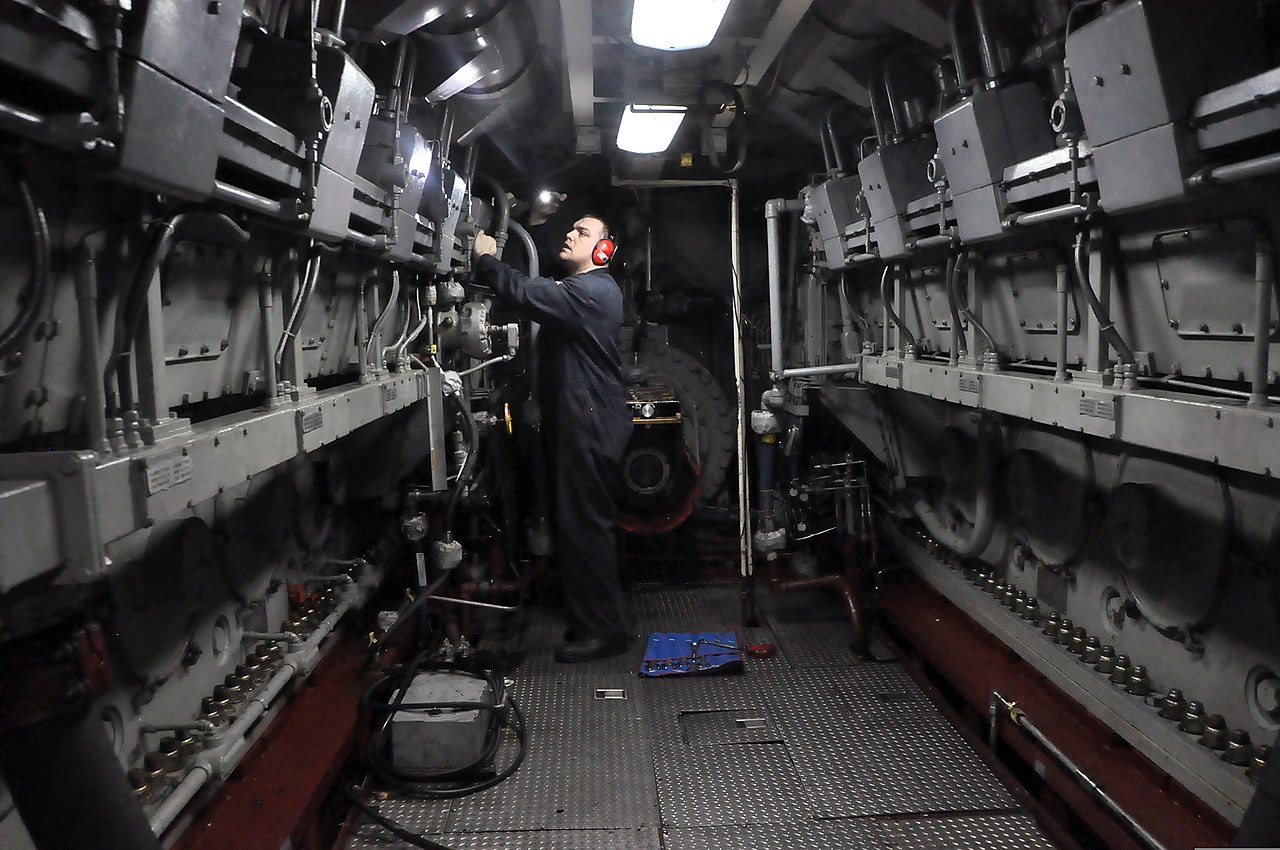
Diesel engines are checked aboard USS San Antonio
The first serious challenger to steam was the diesel engine, which began to go to sea even before WWI. It had three major advantages over steam. First, it was significantly more efficient at turning the energy of the fuel into rotation, with diesels having two to three times the horsepower per unit weight of fuel per hour as contemporary steam engines. Second, they were easier to run and maintain, requiring fewer crew. These two advantages made diesels attractive to merchant ships, although adoption wasn't universal until after WWII. And third, they were far faster to throttle. A boiler could take an hour to produce steam from a cold start if another boiler on the ship was available, and far longer if the entire plant was cold. This often meant that warships had to operate inefficiently, with more boilers online than they needed at the moment in case demand for steam increased. Diesels could be turned on and reach full power almost immediately, then shut down just as rapidly.
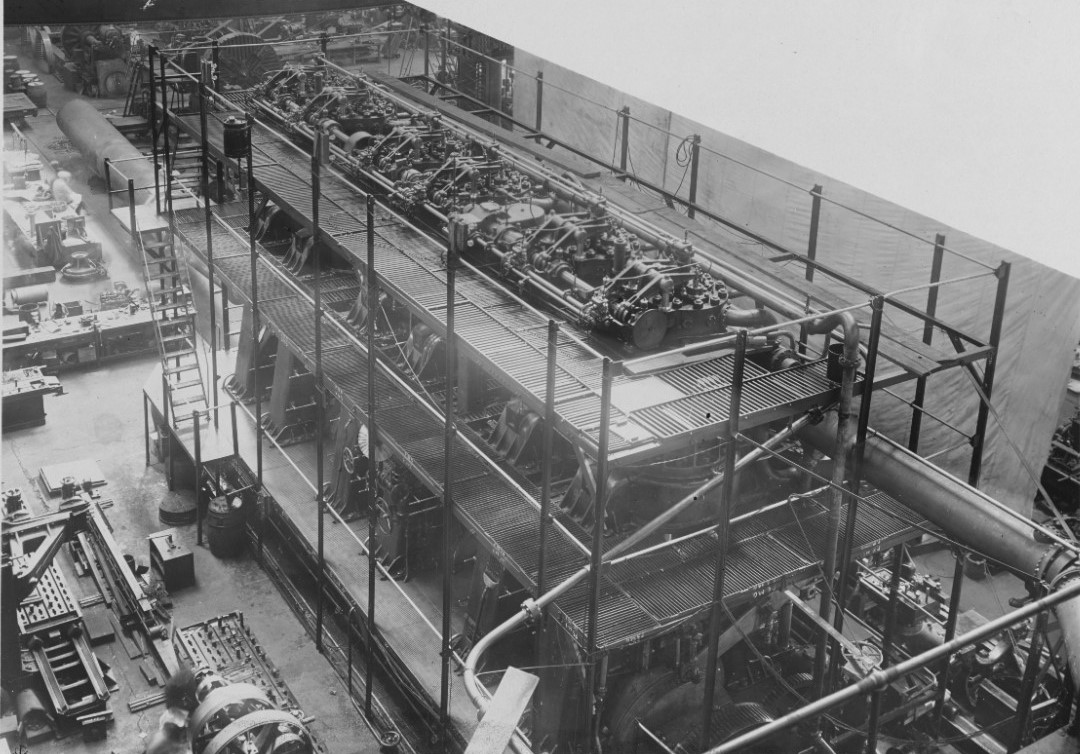
A diesel for USS Maumee, built by a young engineer named Chester Nimitz
Unfortunately, they also had two major disadvantages. First, they were much less powerful per unit weight than steam plants.2 This meant that for most warships, particularly small ones where speed was at a premium, diesels were simply not an option. In theory, they might have been better suited to the large and relatively low-powered capital ships, but their second disadvantage killed off that application. Before WWII, diesels tended to be unreliable, particularly the extremely large and powerful diesels needed to propel big ships. Things were somewhat better in lower-powered designs, which could take advantage of research done for land-based diesel engines.3
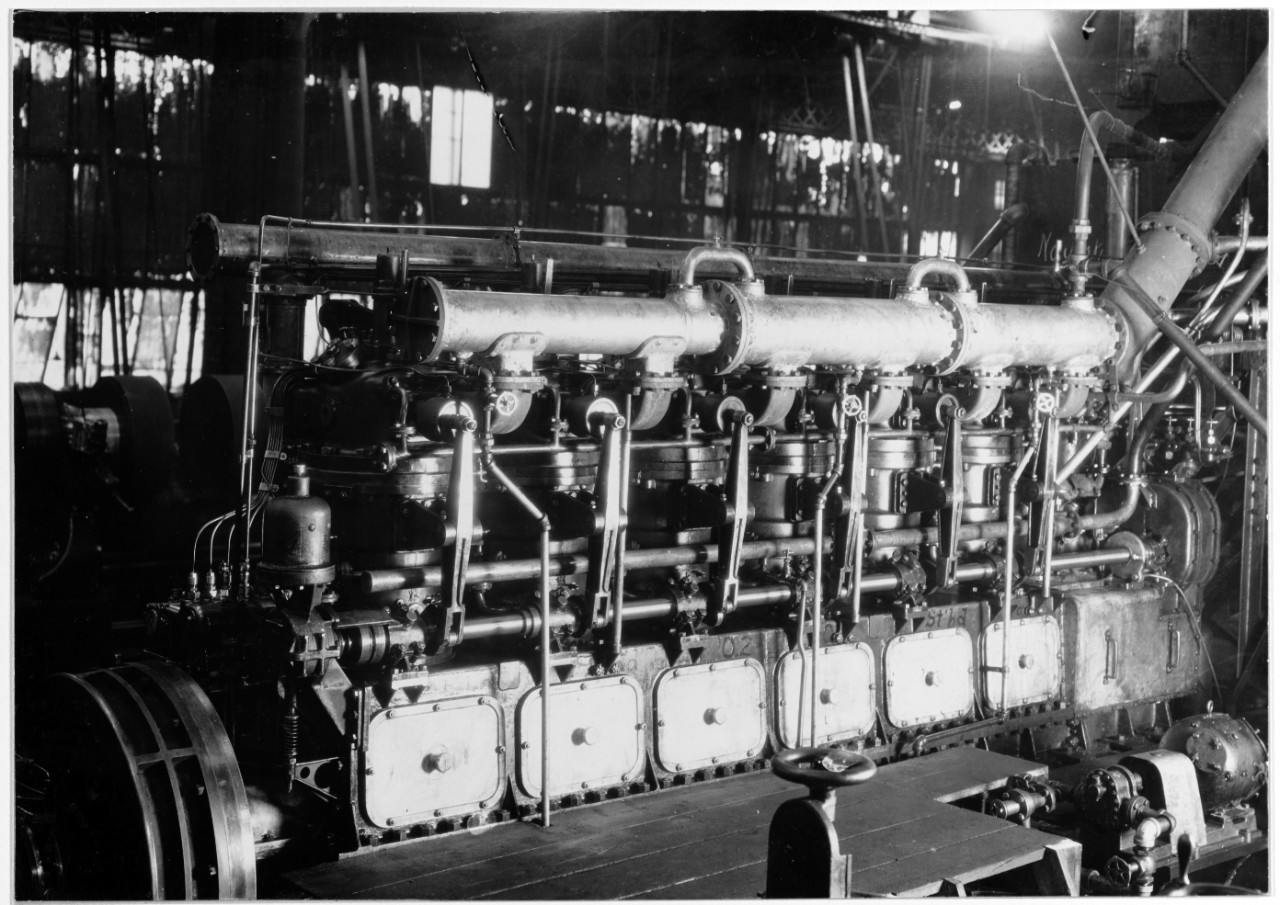
Early submarine diesel for USS O-2
But there was one place where diesels found an immediate niche: submarines. Steam had always been a poor fit for submarines, as the long startup and shutdown times had posed a serious issue for a craft that might have to dive at short notice, and definitely didn't want to sit around on the surface while the plant came online. Most very early submarines used gasoline engines, but the flammability of gasoline meant that it was jettisoned in favor of diesel by 1910, despite the slightly better power-to-weight ratio.4 Diesel was also more efficient, and steam only reappeared in a few submarines intended for high-speed operation with the fleet, most notably the ill-starred British K class. Even today, the primary power source for all non-nuclear submarines is the diesel engine.5
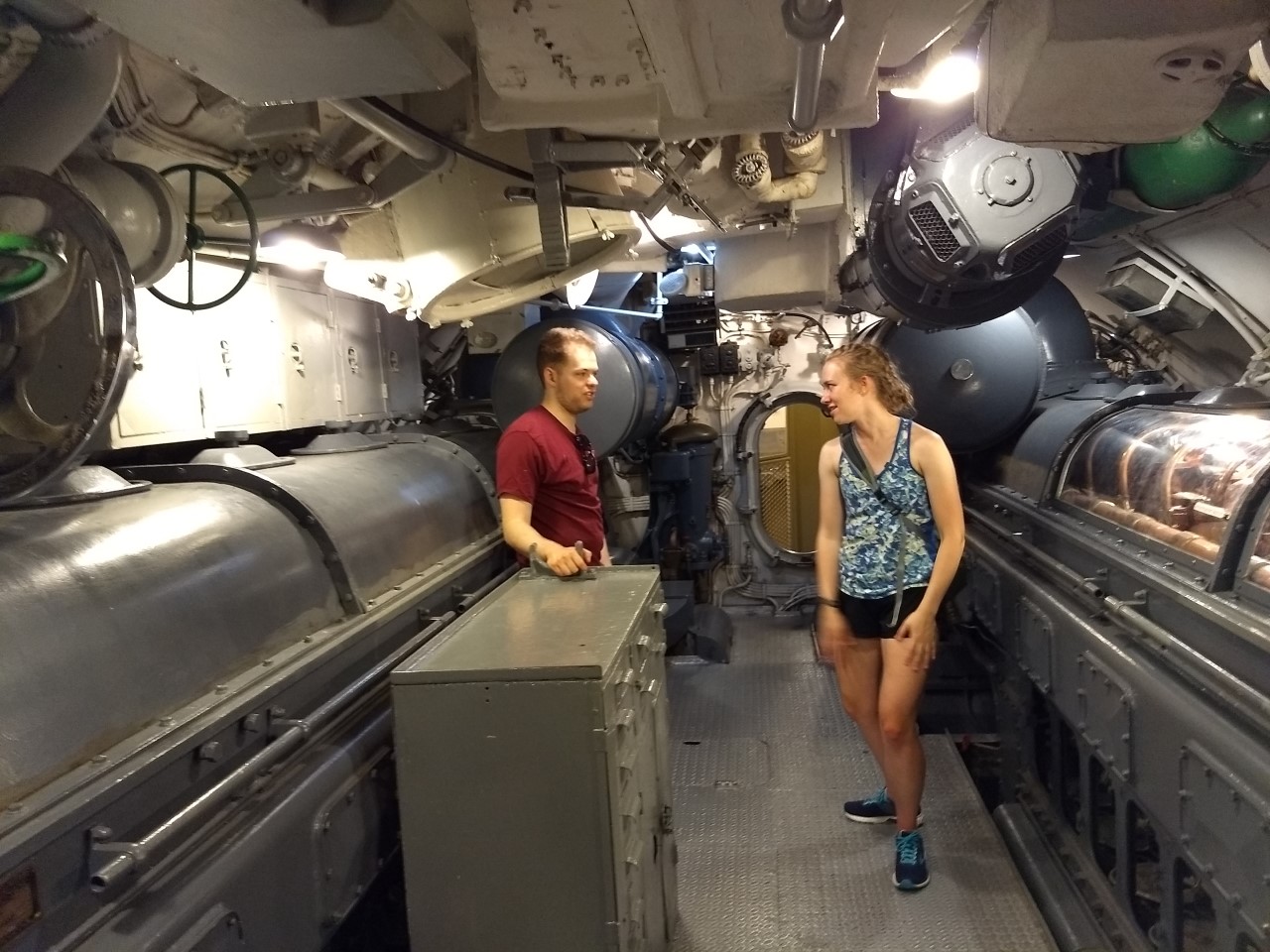
The engineroom aboard Lionfish at Battleship Cove
Most of these submarines had two separate sets of diesels: one that was connected directly to the propellers to provide propulsion on the surface, and another that was connected to a generator to recharge the batteries that propelled the boat underwater. In the early 1930s, the USN, always a leader in such things, chose an alternative approach, where all of the diesels were attached to generators, and power was sent to either the battery for charging or the motors for propulsion as needed. This meant that the plant was somewhat larger and heavier than a direct-drive system, but it did bring several advantages. First, by making the diesels independent of the motors, they could be combined in the most advantageous way, including running the boat on a subset of the engines while others were being worked on. Second, it resolved a problem where if direct-drive diesels were run at a "critical speed", the vibrations on the crankshaft would build up and destroy the engine. Third, it proved very useful postwar. As originally designed, the motors were run at half power underwater and full power on the surface, but when underwater performance became increasingly important after WWII, some fairly simple tweaks, often made as part of the GUPPY program, allowed them higher underwater speed without a major rebuild. Fourth, it isolated the diesels from the rest of the design, and gave builders more options when it came to finding engines. The Bureau of Engineering worked closely with the emerging diesel locomotive industry, and ultimately gave American submariners superb powerplants for their war with Japan.
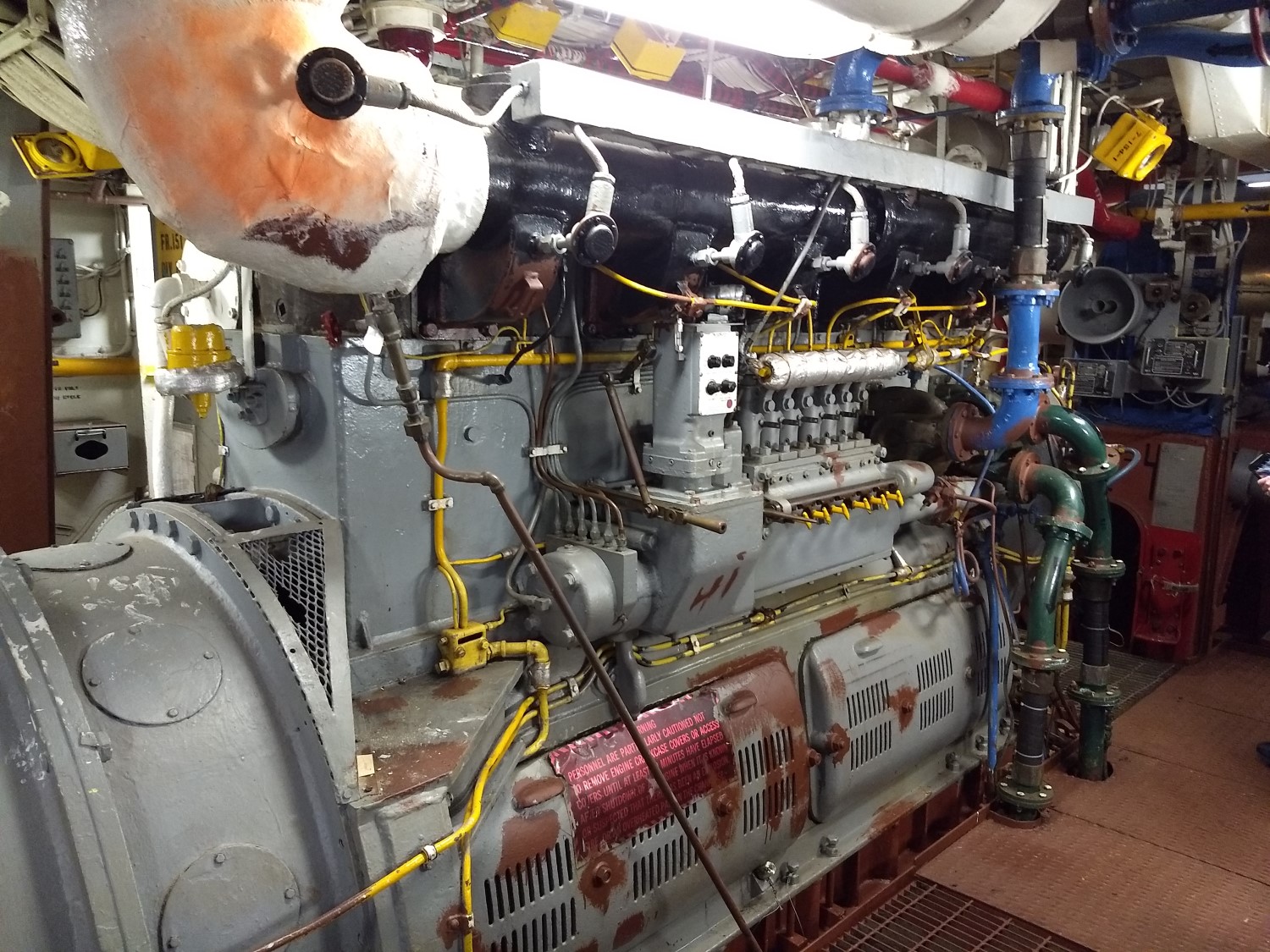
The diesel generator in Iowa's auxiliary machinery room, also derived from a locomotive diesel
Diesels also found wider use on surface ships during the war. Truck diesels powered many small craft, such as the ubiquitous LCVP, while locomotive diesels were used in many larger vessels, thanks to their good reliability and minimal manning requirements. Some, such as the LST, used direct drive,6 large ships tended to use diesel-electric propulsion, with large numbers of diesel generators feeding the motors.7 Most notable were the destroyer escorts, which saw the use of diesel-electric, turbo-electric, geared diesel and geared turbines for otherwise similar ships, based on the ability of American industry to produce the required plants.8
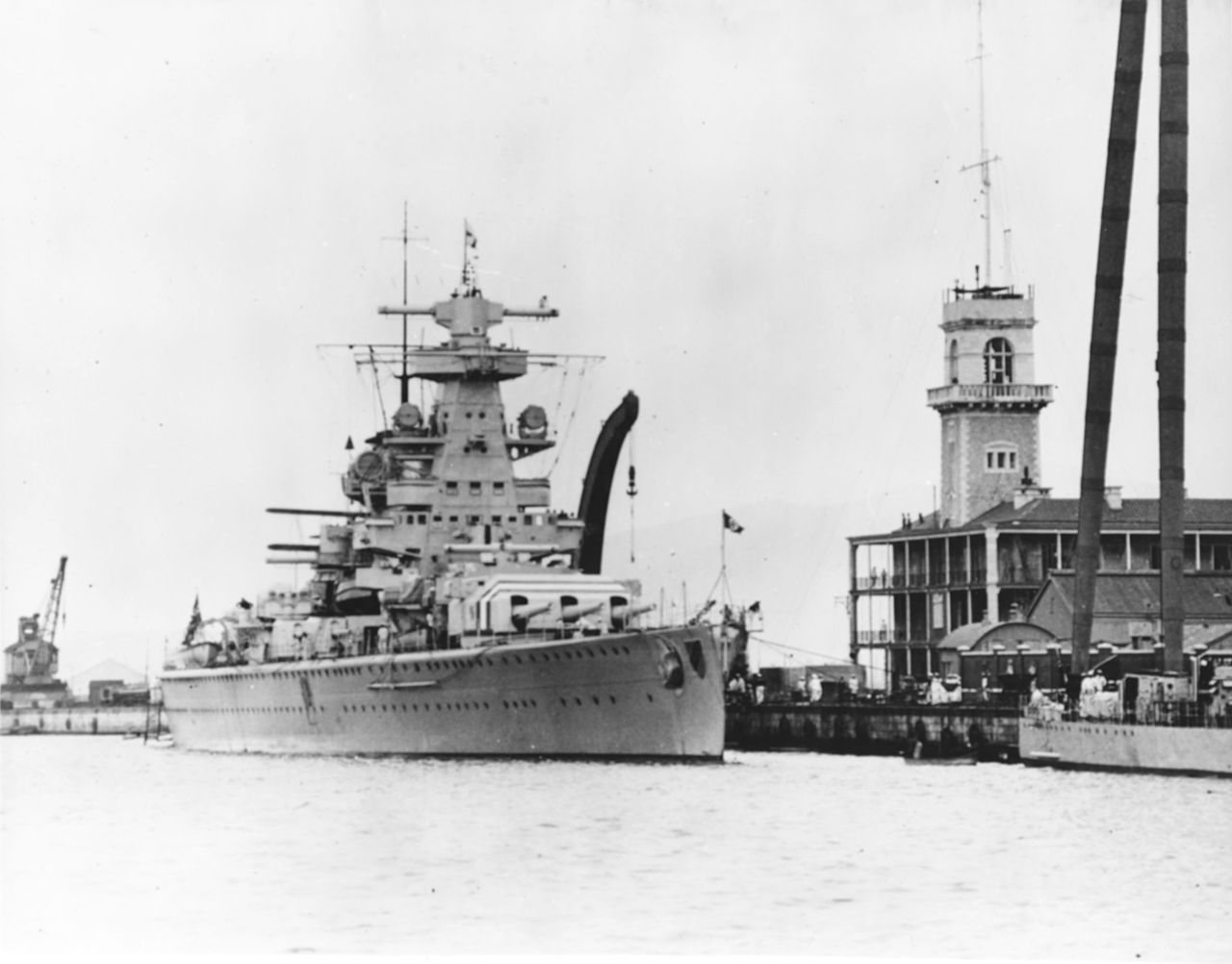
Admiral Scheer of the Deutschland class
But all of these ships used small diesels producing at most 2,000 horsepower, which wasn't really enough for large or fast vessels. Those would require much bigger diesels, purpose-built for marine propulsion. The first major warships to use these were the German Deutschland class "pocket battleships". This was largely a result of their mission as commerce raiders, with the diesels giving a range of 10,000 nm at 20 kts, a distance which even the long-ranged US cruisers could only make 15 kts at. The top speed of around 28 kts took close to 50,000 hp, provided by eight geared diesel engines.9 German leadership in diesel technology meant that the engines were reliable enough, even if they didn't make their designed horsepower, but the ships experienced severe vibration, which rendered much of their fire-control equipment unusable at certain speeds. Design tweaks mitigated this problem, including the development of a special suspension for the forward fire control tower. While modern diesels have less vibration than their 1930s predecessors, this is still a problem, and the USN long considered them unsuited for ASW due to the noise they produced.
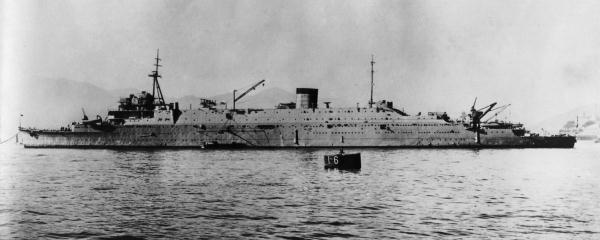
Submarine tender Taigei
Other nations were not so lucky. The Japanese investigated diesels on the submarine tender Taigei with the intention of using them on the Yamato, but they proved horribly unreliable. Given that the developed version would be under 8" of armor, they abandoned their plans, and went for pure steam plants instead. This wasn't as much of a change as might be expected. The original plan had been to install about 60,000 shp of diesels and 74,000 shp of turbines, which would give the designers the best of both worlds, with the endurance of diesels for cruising and the power of turbines for top speed. The Germans, after lots of work on the vibration problem, decided to use diesels on the H class battleships, producing 9-cylinder engines with a 65 cm bore and 95 cm stroke, each capable of producing around 13,000 horsepower. The prototype ran reasonably successfully, but the ships were cancelled with the outbreak of war.
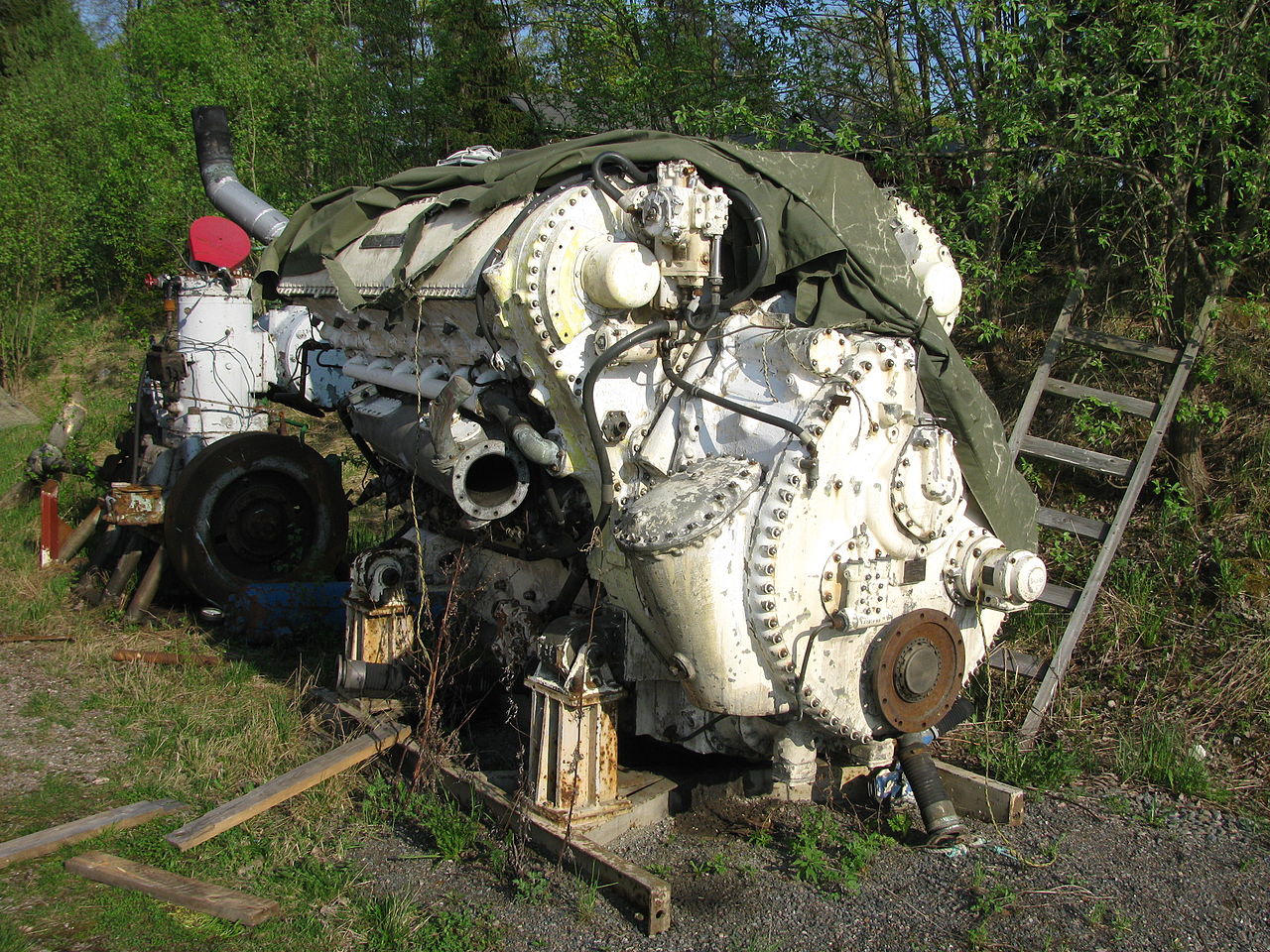
A Napier Deltic engine with three crankshafts, as used on some postwar fast craft
Postwar, heavy marine diesels came to dominate the merchant fleet, and high-speed diesels replaced gasoline engines as the propulsion of choice for fast attack craft. Low-speed marine diesels became common in many auxiliaries, but adoption in the main line of surface warships tended to be limited by the low power-to-weight ratio of the engines. They are more common in ships where running cost is more important than outright power, such as the sort of frigates that end up in the hands of second-rate navies, or in cases where they could be combined with other engines to maximize their virtues. Instead, the big winner of the postwar years in naval propulsion was a derivative of the engine that was revolutionizing aviation: the gas turbine. We'll look at it next time.
1 This isn't to say that conventional steam didn't see more development. In the US, steam conditions reached 1200 psi and 950°F, and experiments were made with pressure-firing, which is essentially like turbocharging for boilers. The 1200 psi plants were not particularly reliable, and pressure-firing was even less so, although the Soviets used it quite a bit. ⇑
2 Pinning down exact figures on this proved far more difficult than expected. On the basis of a number of comparisons in the 1900-1920 period, I got anywhere from "about the same" to "over an order of magnitude better for steam". I don't think either is correct (doing naval weight comparisons is hard) but I suspect the actual advantage for steam was probably in the 3-5x range early, falling some as time went on. ⇑
3 Diesels did find immediate acceptance in auxiliary roles. The British first adopted them to provide power while ships were in port with their boilers shut down. The USN (and ultimately most other powers, including Britain) used them as emergency generators to make sure that the ship wasn't totally disabled if the main steam-powered generators went down. ⇑
4 Gasoline engines were only used in the most power-critical applications, such as PT boats, where the craft themselves were more or less expendable. These were usually aircraft engines, which allowed them to take advantage of the latest developments in that field. I'm not sure if there are some inherent problems with extremely large (multi-thousand horsepower) gasoline engines that prevented them from being used in larger warships, but I wouldn't be surprised if that was the case given the dominance of diesel in the field. Or it could just be the fire hazard. ⇑
5 Some boats use systems that allow them to recharge their batteries without oxygen, but none of these have nearly the energy density or low cost of diesel fuel, so that's used in non-tactical situations. ⇑
6 Note that direct drive for diesels means something different than for steam turbines. With steam turbines, direct-drive means that there's no gearing between the turbine and the shaft, while with diesels, direct-drive means that it's not diesel-electric. ⇑
7 The big difference from submarine practice was the lack of any battery. ⇑
8 An amusing side-note to the diesel propulsion story is the Claud Jones class of American destroyer escorts. Intended as a mobilization design and built to use components that could be mass-produced, it turned out that the diesels required more volume to produce less power than the contemporary steam-powered Dealys, which made the ships too slow to hunt fast submarines. To make matters worse, the gears required were of the size that they expected would be a bottleneck, so the whole program was abandoned after four ships. ⇑
9 One reason that almost all of these designs have so many engines is that heavy diesels are not particularly efficient outside a relatively narrow band. The best way to throttle is to simply cut in an extra engine, which is made easier by how quickly diesels can be throttled. ⇑
Comments
Why on earth would you build a 9 cylinder engine if you were worried about vibration problems!?! Why not an inherently balanced engine layout?
Because it's the Germans doing it, and they can never go for the simple solution when the complicated one will do.
More seriously, my source on this says that they were able to solve the vibration problem by careful design of the engine mounts, and so they presumably were willing to go for the optimum on the engine itself. Or the people doing the ship as a whole couldn't tell MAN (who I believe did the diesel) to stop being stupid and pick a lower-vibration design. That also seems plausible for Nazi Germany.
cassander:
No such thing with a two stroke (and they were already using 9 cylinder engines on the Deutschland class so seem to have been confident they could deal with the problems since they'd just done it).
steam only reappeared in a few submarines intended for high-speed operation with the fleet, most notably the ill-starred British K class
Though the link to Wiki from footnote 5 tells us about the French Scorpene class, their current model, that uses steam engines running on ethanol and bottled oxygen.
If you really want to be pedantic, the world submarine fleet is second only to the carrier fleet in the prevalence of steam, because that's how nuclear plants work. I intend to cover AIP systems at some point, but I stand by the statement within the bounds I was looking at here.
Interesting to hear about. I wasn't aware that France also operated non-nuclear submarines, and thought that it was basically just Russia and China that operated a mix now. I know that the US and UK used to have both, but have since moved to an all nuclear fleet. Any idea why France hasn't?
They actually don't. France essentially funds its military development by exporting stuff and making its own military use similar systems, although in the case of submarines, they get SSNs while most customers (except Brazil) get SSKs. The AIP system Doctorpat describes is designed as a drop-in reactor replacement for export subs.
As a former supply officer I worked with once noted: "Nuclear: a really expensive and dangerous way to boil water."
The problem with large gasoline engines is the fuel efficiency of diesel engines becomes too important. For a lawn mower or small car the difference between amounts of fuel burned isn't a big part of the budget and so nobody cares, and some of the performance advantages of gasoline is worth it. However for larger engines even if the cost of fuel isn't a line item, the time to refuel, or the storage space for the fuel are important issues. As a result all of the really large engine development is in diesels.
It would be interesting to speculate on a world where airplanes never got the jet engine working. Gasoline's power to weight advantages would be important, and there is more than could be done even before computers. In the most ideal case a gasoline engine is slightly more efficient than a diesel engine, but if you leave that ideal case even slightly your efficiency drops much faster than a diesel. If gasoline was required for modern airplanes (think of a 777 with props...), ships probably could benefit from the development on those large engines.
bean:
If you wanted to be extra pedantic you'd note that there are more real submarines than carbon neutral flattops and that nuclear gas turbines have been built (though not many and none naval).
bluGill:
Probably a move to two strokes which with direct injection can be about as efficient as four strokes while having more power with long range aircraft having two stroke diesels.
The Wankel engine would probably also show up though it'll take some time for the problems to be solved.
In terms of engine configuration the Wasp Major was a nightmare so engines bigger than a two row radial are likely to end up as liquid cooled inline radials and sleeve valves seem to have reached maturity.
bluGill:
Nope, diesel combustion is inherently more efficient.
bluGill:
The Bristol Brabazon had 8 engines (Bristol Centaurus, probably the most powerful aircraft piston engine with acceptable reliability) with a lower MTOM than even the 767-200.
But as I said before, without gas turbines long range aircraft end up with two stroke diesels.
@bean
Thanks. That's a pretty impressive sounding export program. Especially Brazil's purchase of the nuclear variant. France's defence industry seems to do well compared to much of the rest of Europe, and their procurement looks to be relatively well planned (Charles de Gaulle excepted).
@Anonymous
Yes, but if we're going to be that pedantic, I'd point out that there's no such thing as a carbon-neutral carrier, because the noisy things on top use a lot of fossil fuels.
@Alexander
Everyone else starts by designing military hardware to their standards and then asking if anyone else wants some. France tends to do it the other way around, and their military gets stuck with what will sell on the export market. The most notable example is probably the AMX-30 tank, which had nowhere near enough armor for fighting the Soviets, but was perfect for export, and sold very well in that market.
bean:
Guess we'll have to wait for synfuel plants that can fit on a carrier (and somehow not violate US Navy fire safety standards).
@bean I suppose that it would be too much to expect to make gains on the export front without any tradeoffs elsewhere. Regarding the AMX-30, wasn't there a period where the development of HEAT warheads lead to designers favouring lighter, faster tanks? The German Leopard was a relative of the AMX-30 (as the Leopard 2 is to the M1) and had broadly comparable armour. Then again, I think it also achieved export success, so perhaps that was the explanation for both designs having less protection?
That's a good point. I was basing this on a comment in Friedman's The Fifty Year War, and he may have overstated his case. On the other hand, the Leopard I was 15% heavier than AMX-30 (which can make a big difference) and most of its export success was to other NATO countries. The buyers outside NATO were all in South America, and Brazil and Chile have reputations for being the better buyers of weapons in that sphere, at least these days. AMX-30 was only bought by Greece within NATO, and several countries not known for their discrimination in purchasing outside of it. Greece definitely and Chile probably used Leopard I to replace AMX-30, which suggests they're less comparable than we might think.
@Anonymous
Most people think that the diesel engine is more efficient, but this isn't true. They are both governed by the same Carnot laws, and so the theoretical efficiency of each is the same. Lower compression allows for slightly more efficiency in that theory.
The reason for the myth is in the real world things are not ideal.
A gas engine at low rpms (different engines have a different low RPM speed) and full throttle the gas engine is at its best, but full throttle means maximum power which is either going to increase your RPM outside of the ideal range, or you have such a high load that the issues with sustained max load mean the engine cannot last very long, either way a gas engine is basically never operating close to ideal efficiency, while a diesel takes to low throttle better and so is running at closer to the ideal efficiency for the given load. Even at that it is known in the generator world that a diesel running at 80% of full load will use less fuel than running at 50% of full rated load.
The other issue is diesel fuel has more energy per volume vs gasoline. So even in the rare case when the gasoline engine is in the band where it is more efficient that a diesel, it still needs to use 1/3rd more fuel to get the job done.
@bean Synfuel might be better for fire control. We will have to see what the input to synfuel is, and how fast they can produce it. If the input is not very flammable/explosive (compared to whatever jet fuel they use), and the plant is the pump, this could be a win - no jet fuel is stored on board, they just make it one demand. However this probably requires far too much energy. Most likely they only store as much fuel as needed for the worst case, which is governed by how many missiles/bombs on board before they have to leave the battle, and then refill those tanks while going to/from the resupply points. (which in turn implies the synfuel plant could be an auxiliary a few days from the main action)
The future will be interesting. So many ways it can all work out.
@bluGill
First, a note of pedantry. Fire control refers to the process of making sure that your weaponry lands where it's supposed to. Damage control is the bit where you make sure your own ship doesn't catch fire or blow up.
I was initially a bit suspicious of the thermodynamic feasibility of JIT fuel production, but some quick math makes it look more reasonable than expected. If I my numbers are right, a carrier's reactors produce energy (shaft hp, not raw thermal) equal to that of a Super Hornet's internal fuel load in 1.3 seconds. Obviously, you'd want a lot of that energy for other things and the conversion won't be 100% efficient (but your starting material might also not be at thermodynamic zero) but it's not implausible that it could create fuel essentially as it's needed, modulo an hour or two.
But to be pedantic again, jet fuel isn't that much of a fire risk. It's a lot less dangerous than avgas, which made the introduction of jets on carriers a lot easier because they could use a lot more tankage.
I think your numbers are a bit off there.
A Super Hornet's internal fuel load is 6,667 kilograms. The DTIC specification for JP-8 is 18,400 btu/lb heat of combustion, and because the British suck at inventing thermal (or other) units, 1 btu/lb = 2326 J/kg. So, the energy content of a Super Hornet's internal fuel load is 6,667 * 18,400 * 2326 = 2.85E11 Joules.
A Nimitz is rated at 260,000 shaft horsepower, and see above re Imperial units, one horsepower = 745.7 Watts. That gives 260,000 * 745.7 = 1.94E8 Watts shaft power.
2.85E11 / 1.94E8 = 1,469 seconds to theoretically synthesize enough fuel to fill a Super Hornet's tanks.
Maybe two planes' worth per hour while still making modest speed and covering housekeeping requirements. With a perfectly-efficient synthesis, but maybe we can handwave using raw thermal power as process heat and have those effects cancel.
Not completely out of the question, but probably not practical. Now, about my proposal for the all-electric TeslaHornet and the bit where we coat the flight decks in ruggedized solar panels...
Ack. I must have dropped three orders of magnitude somewhere. Thanks for catching that. The Fords are supposed to manage 160 sorties per day, so there's no way the onboard reactor will be able to synthesize enough. Not to mention the complexity of the machinery.
bluGill:
But you think it isn't and that's not true.
bluGill:
The maximum theoretical efficiency at the same compression ratio is the same, but diesel engines operate at much higher compression, they need the compression to ignite the fuel while petrol engines would knock if you compress too much.
bluGill:
The equations show the exact opposite, that Carnot efficiency is dependent on compression ratio and increases as that increases.
bluGill:
Yes, which makes diesel have even better fuel economy but even if you compare per energy content of fuel the diesel is still more efficient.
bluGill:
Synfuels would only make sense with nuclear so you're not going to be putting it on anything dino burning.
bean:
The worry isn't that the jet fuel will burn, but that the chemicals in the intermediate stages will burn.
The first stage is going to involve splitting water to hydrogen and oxygen and then reacting that hydrogen with a carbon source obtained from turning CO₂ into something else (probably CO).
No worse than things the chemical industry does everyday but it might be a hard sell to those who ban anything with JP-8 in it from the hangar.
John Schilling:
bean:
That's 48 sorties a day so it's still within the realm of technical possibility, though it would require a significant scale up of the reactor to meet that many sorties per day.
Realistically if you were doing it you might want something better than a PWR, some of the Gen IV designs could combine higher power density with increased temperature.
John Schilling:
Be careful, someone might make the US Navy build it.
There's nothing stopping you from putting a nuke plant on an auxiliary if you need to. It doesn't make sense a lot of the time, but it's possible.
Yeah, that's not going to go over well at all. They'll just say "nope, not here" and keep doing what they're doing.
Every single person in Naval Reactors would tell you that will happen over their dead body. This is an organization that makes the John Birch Society look liberal. More details on Wednesday.
A lithium-air battery has a theoretical maximum of 12 kWh/kg, which is about the same as for jet fuel. So in theory, if you made a really really good battery with no extra weight in the housing or internals, the TeslaHornet could fly.
However, the recharge speed would still be the same, so you'd also need to install a few PowerWalls in the carrier to give it the reserves for constant sorties.
@John
Interesting comparison. My takeaway from this is that, when a conventional carrier is conducting flight operations, its air group will be burning more fuel than it is.
Looks like a Ford-class stores about 1.3 million gallons of jet fuel, which is about 4300 tons. I'm not sure if removing a lot of that tank space would add enough space for the necessary nuclear power, but it'd probably help some.
The one I wonder about is how much air you'd need to filter to get the necessary CO2(since that's presumably your carbon source for this, if we're making an eco-CVN). 6667 kg of fuel per Hornet is 5614 kg of elemental carbon, which is 20,586 kg of CO2. CO2 is about 410 ppm in the atmosphere, which means about 50,000 tons of air needing to get filtered per fighter you load up. That's about 41 million cubic metres of air at sea level.
At 160 sorties per day, you'd need to filter about 76,000 cubic metres of air per second to extract the necessary CO2. That's likely to create a wind far in excess of the worst hurricanes in history, even if your air intake was the size of the carrier itself. And that assumes you extract every single molecule of CO2. Yeah, this isn't practical.
The studies I've seen eg. https://www.zmescience.com/research/us-navy-synthetic-jet-fuel-seawater-0423432/
They were planning on getting both the hydrogen AND the CO2 from the seawater.
Seawater already concentrated CO2 to a significant extent compared to air, so your mass flow rate required to get enough carbon is greatly reduced.
bean:
Need to find a way to go from water and CO₂ to JP-5 without going through any flammable intermediates, maybe the chemical engineers can figure out a way to do it.
bean:
Never mind that it's probably the only way to get costs down enough for an all-nuclear Navy to happen which they do want.
beleester:
That's half way (or more) to being a fuel cell (also Li is highly reactive, I doubt the US Navy would want large amounts of it on their carriers, especially in a form that Air (and potentially water) could easily get to it).
Alsadius:
That's a cube 42.4 m each side.
Getting it from sea water does seem a better idea.
Another possibility but without any environmental benefits would be to store the carbon locally as coal but that probably won't save enough storage space to be worth doing.
Seawater CO2 looks a lot better, yeah. A quick google is 2.3 mmol/kg of inorganic carbon, or an astonishing ~2.7% by mass. (I'd have guessed a dozens of times less, which is why I assumed it'd be atmospheric.)
You'd only need about two million litres of seawater per Hornet (assuming 100% extraction efficiency), or 3850 L/s of flow rate. That's a pipe with a cross-section of a square metre with a flow rate of 4 m/s, which is actually quite sane. Realistic process considerations mean several times that, but that's still not a lot for a carrier. Their reactor cooling needs are probably at a similar scale already.
And yeah, storage as coal is worthless. Carbon is like 85% of the mass of a liquid hydrocarbon, and the process engineering requirements, plus the difficulties of dealing with coal, make that terribly unrealistic.
@Alsadius
That 2.3 mmol/kg is 2.3 millimoles of inorganic carbon per kg of seawater, or 0.0028%, three orders of magnitude less than your figure. It's still more carbon per unit volume than in air, though, by a factor ~100.
Gah, of course. I figured that was way too much, but couldn't find my error.
This is one reason I vomit data into posts like that - kindly strangers catch my mistakes when I give them enough breadcrumbs.
On the other hand, that makes for some interesting operational abilities regarding the necessity of making wind over the deck for flight operations :D
Never want to say impossible, especially somewhere John Schilling might read, but...are you sure you can't tolerate just minimizing the inventory of intermediates, the way we do with Methyl iso-cyanate? It's a lot more straightforward if we can go with 'minimize'.
Minimizing would help but the US Navy is notable for being extremely paranoid about flammable stuff so still might not meet their approval.
It's possible that doing it on shore and transferring it on auxiliaries might be the way to make the planes carbon neutral, just like the way to make nuclear powered trains isn't to put a reactor on a locomotive but to put wires above the track.
I was an EN2 on two LSTs and a Destroyer. For shore duty I had the privilege of rebuilding a Detroit Diesel from the block up. I enjoyed it completely. Never used my experience after the Navy wish I had.